Wind Energy End-of-Service Guide
An informational resource for communities to better understand repowering or decommissioning processes for wind turbines and related infrastructure.
Introduction
Overview
The Wind Energy End-of-Service Guide is intended to give a foundational understanding about what happens to wind turbines and related infrastructure when a wind energy project is repowered or decommissioned.
As of October 2022, over 70,000 land-based wind turbines with a combined capacity of nearly 138 gigawatts (GW) were installed across the United States, with more being deployed to reach state and federal renewable energy goals.[1] While some of these wind turbines are newly installed, others are part of an aging fleet that is coming to the end of their expected design life and will need to be partly or fully repowered to extend their life or be decommissioned (which removes a wind energy project and involves land restoration). So far, more than 14 GW of U.S. projects have already been fully or partially repowered with analysts expecting an additional 16 GW of full or partial repowers through 2026.[2]
About This Guide
The Wind Energy End-of-Service Guide is divided into four sections.
The Life of a Turbine section focuses on the service life of a wind turbine, what happens when they reach end of service, the overall recyclability of a project, and what is being done to improve recyclability.
The Repowering section focuses on replacing components or full turbines with newer technology, how these activities can potentially change turbine and project characteristics, as well as the local impacts from repowering wind energy projects.
The Decommissioning section focuses on project removal, site restoration, and the local impacts from the decommissioning of wind energy projects.
Finally, the Blade section of this resource focuses on how many blades will need to be processed from wind energy projects, how they are processed, and the issues and concerns related to the landfilling and recycling of these components.
This work was authored by Frank Oteri, Heidi Tinnesand, Chloe Constant, and Matilda Kreider (NREL).
Acknowledgments
Thanks to the U.S. Department of Energy (DOE) for the financial support to create this guide and to DOE staff, the National Renewable Energy Laboratory (NREL), and the web development team for creating this website and making this guide possible:
- Jen Grieco, Sheri Anstedt, Laura Carter, Josh Bauer, and Al Hicks (NREL Communications)
- Joy Page, Maggie Yancey, Tyler Christoffel, Shaelyn Patzer, Rin Ball, Heather Doty, and Liz Hartman (DOE).
This work was authored by the National Renewable Energy Laboratory, operated by Alliance for Sustainable Energy, LLC, for the U.S. Department of Energy (DOE) under Contract No. DE-AC36-08GO28308. Funding provided by U.S. Department of Energy Office of Energy Efficiency and Renewable Energy Wind Energy Technologies Office. The views expressed in the article do not necessarily represent the views of the DOE or the U.S. Government. The U.S. Government retains and the publisher, by accepting the article for publication, acknowledges that the U.S. Government retains a nonexclusive, paid-up, irrevocable, worldwide license to publish or reproduce the published form of this work, or allow others to do so, for U.S. Government purposes.
The Life of a Wind Turbine
Duration
How long do wind turbines last?
The expected service life of wind turbines is approximately 30 years.[3] This does not mean that every individual turbine component is designed to last for 30 years. While foundations and towers are expected to meet that timeline, blades, gearboxes, generators, and other smaller hardware may need to be repaired or replaced earlier. Replacement and repairs usually occur when a component has reached or exceeded its operational lifetime or because of excessive operational wear and tear. In addition, many components are upgraded as part of repowering.
End of Service
What happens to components at end of service?
When wind turbine components and project-related infrastructure are taken out of service, they can be processed through one of three methods—repurposing, recycling, or disposal:
Repurposing is the use of components, or parts of components, to create new products— like pedestrian bridges, playgrounds, benches, bike shelters, affordable housing, and noise barriers (see Figure 14).
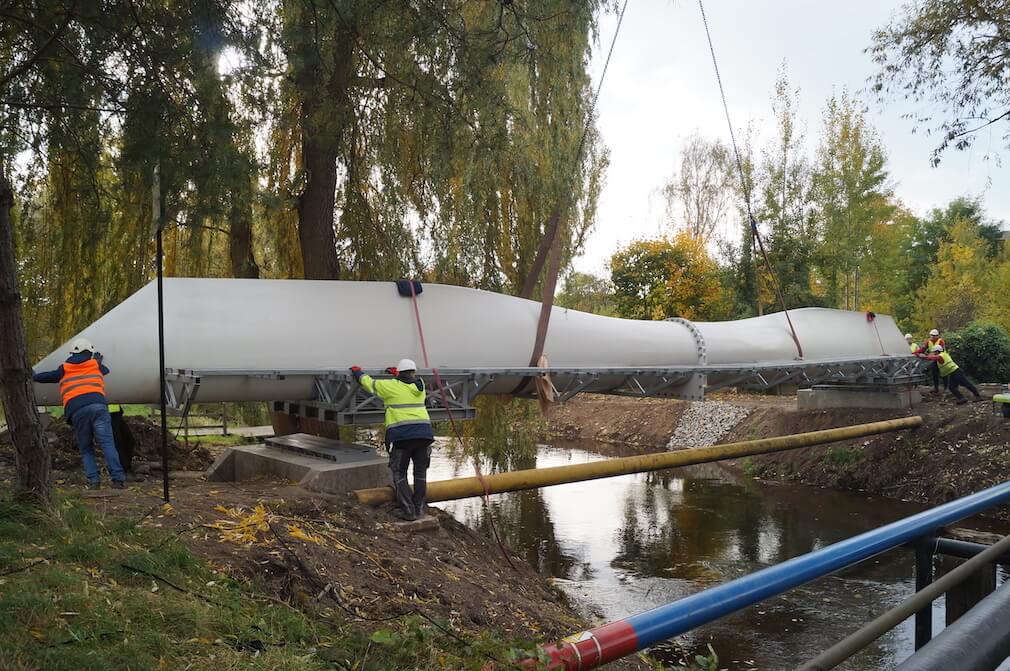
Figure 1. Construction workers install a footbridge across the Szprotawa River in Poland. The footbridge was designed and constructed by Anmet, a Polish recycling company, whose designs feature repurposed wind turbine blades. Photo from Anmet.
Recycling involves thermal, chemical, or mechanical processing that transforms components into materials that can be used in new products, like cement or new wind turbine blades (see Figure 2 and 3).
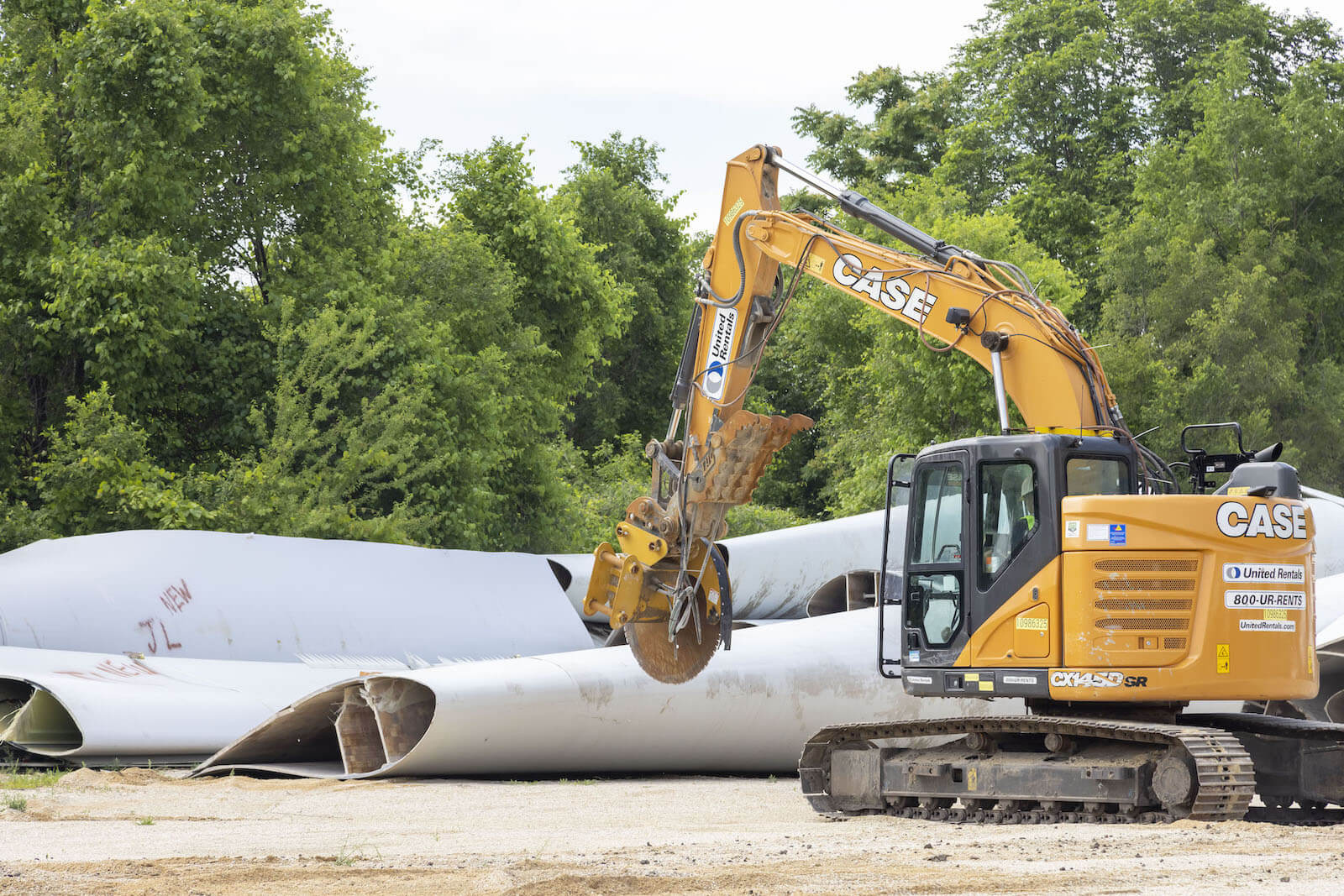
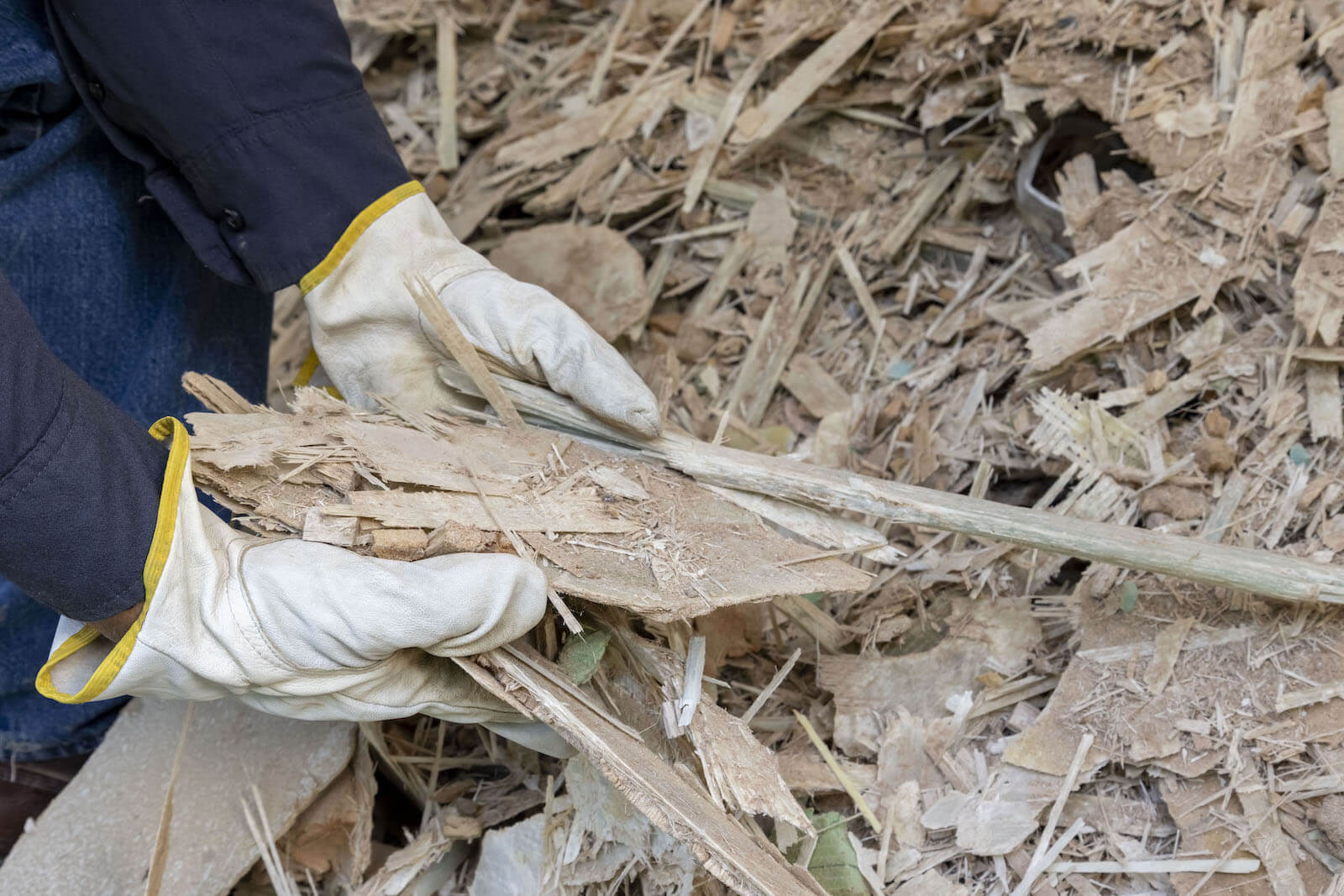
Figure 2 (left) and 3. The image on the left shows wind turbine blades being segmented for mechanical recycling at Veolia’s blade recycling facility in Louisiana, Missouri. The image on the right is the final product that is realized when the mechanical recycling process is complete. Photos from Veolia
Disposal usually involves landfilling components, but it can also include incineration or leaving in-ground components in place.
The way in which a component can be processed depends primarily on the materials it is made of. However, other factors, like local and state regulations; market demand; costs; availability of recycling and processing infrastructure; and land and permitting agreements, will ultimately influence how components are processed (i.e., repurposed, recycled, or disposed of).
Recyclability
How much of a land-based wind turbine/project is currently recyclable?
The metal components that make up most of a wind turbine's mass are easily recyclable and often considered a salvageable material with monetary value. Composite components (like blades, nacelle covers, and rotor covers) are more difficult to recycle. In addition to wind, composites are used in a variety of industries like automotive, aviation, construction, infrastructure, and in many consumer products. Made from fiberglass or carbon fiber mixed with epoxy resin, composites are designed to be lightweight and durable. Regardless of industry, composite components have historically been disposed of in landfills when they have reached their end of service. Mechanical recycling (i.e., shredding or grinding composite materials) and other processes that European countries have used as disposal alternatives are increasingly being used in the United States. For instance, the Veolia facility in Louisiana, MO has been expanding the number of blades it processes on an annual basis. As of the fall of 2020, the facility had mechanically recycled more than 100 blades.[4] Currently, the facility can mechanically recycle 3,000 blades/year.[5] Additionally, researchers are developing new domestic recycling and repurposing solutions for blades and other composite components.
Between 85% and 90%[6],[7] of a wind turbine's mass (excluding the foundation, underground wiring, and other project-related infrastructure) is made up of materials that are easily recycled, including the aluminum, steel, copper, and iron used in the turbine tower and components housed in the nacelle. Only 6%–14%[8],[9] of a wind turbine's mass is made up of composite components, like blades, nacelle covers, and rotor covers, which are currently more difficult to recycle.
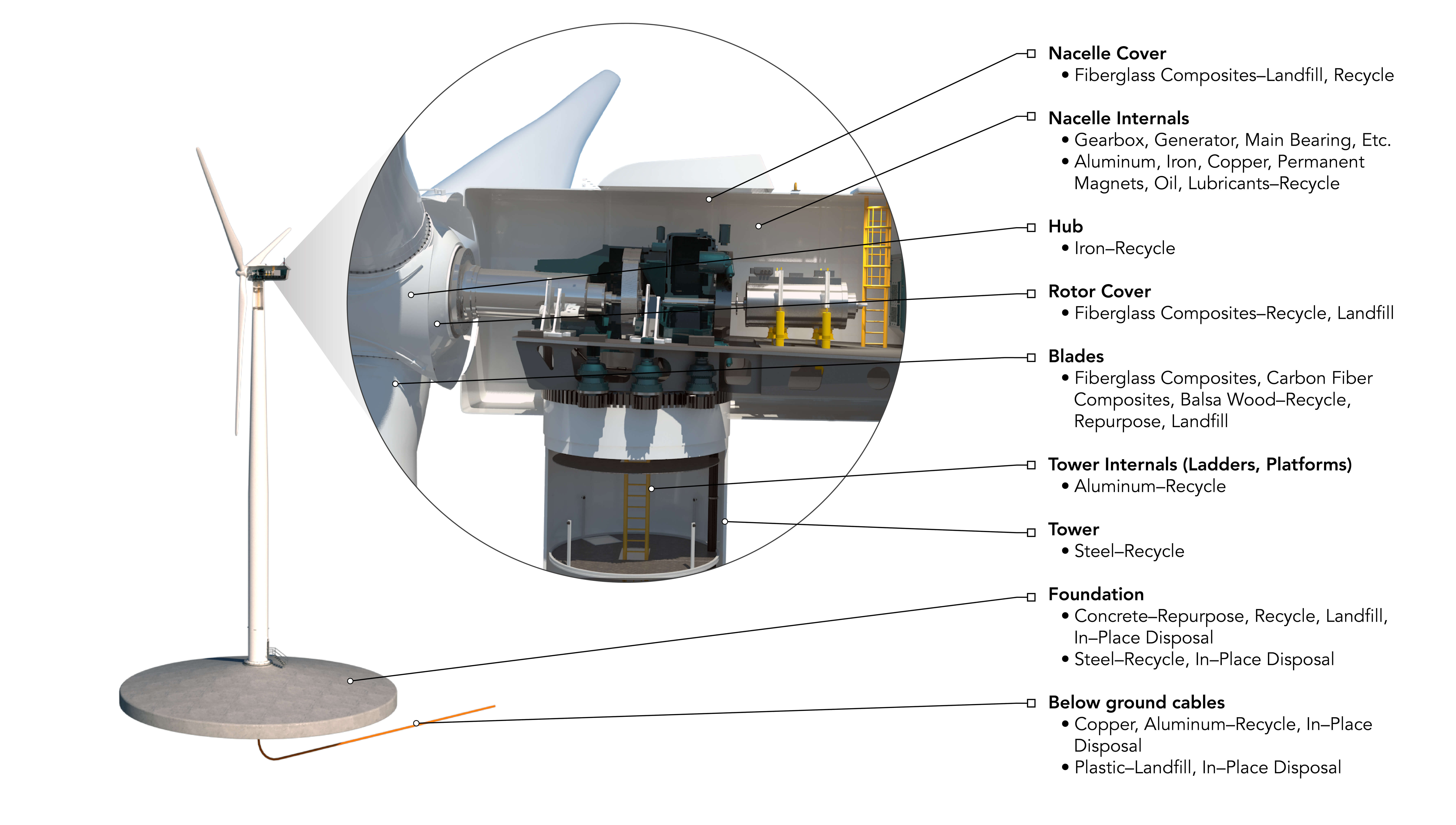
Figure 4. This diagram identifies different wind turbine components and project related infrastructure, the materials they are made from, and how they are processed when a wind energy project reaches its end of service. Image by Josh Bauer, NREL
The infrastructure (e.g., foundations, underground cables, access roads) associated with wind energy projects has its own end-of-service considerations, including the partial in-place disposal of foundations and the full in-place disposal of underground wiring (see Figure 4). When associated infrastructure is included, 75% of the mass of a land-based wind power project is attributed to foundations, whereas 2% is attributed to cables, and the remaining 23% is attributed to the wind turbine.[10] While foundations (see Figure 5) and cables can be recycled or repurposed, they are typically left in place in the ground below a depth (usually 3–5 feet) that is agreed upon by the community/landowner and project owner(s) due to environmental impacts associated with complete removal. Environmental impacts during decommissioning/full removal of below-ground infrastructure can include noise disturbances, ground disturbance, and more. Additional environmental concerns related to full foundation removal may include compromised site stability, erosion, or unwanted pathways for surface and sub-surface water - due to inappropriate backfilling of the site.[11]
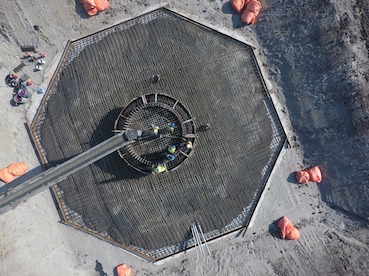
Figure 5. This foundation is part of the project infrastructure at the Amazon Wind Farm U.S. East, located in Pasquotank/Perquimans counties, North Carolina. Photo from Avangrid Renewables
Ongoing Work
What steps are being taken to improve the recyclability of a wind turbine?
While blades and other composite components have historically been processed through landfilling, turbine manufacturers, DOE, universities, and other research institutions have been working to innovate processes and create partnerships that push wind turbines toward full recyclability. In this case, wind turbine recyclability focuses on the turbine itself and excludes project infrastructure like foundations, cables, and access roads.
In fact, researchers at NREL are developing new materials that can be used to manufacture blades that are more readily recyclable.[12] Additionally, many wind turbine manufacturers have announced efforts that will allow them to deploy zero-waste or recyclable blades within the next decade (see Figures 6 and 7). While these solutions will not impact composite components that are already installed at wind energy projects, there are options that can keep currently utilized materials from entering the waste stream.
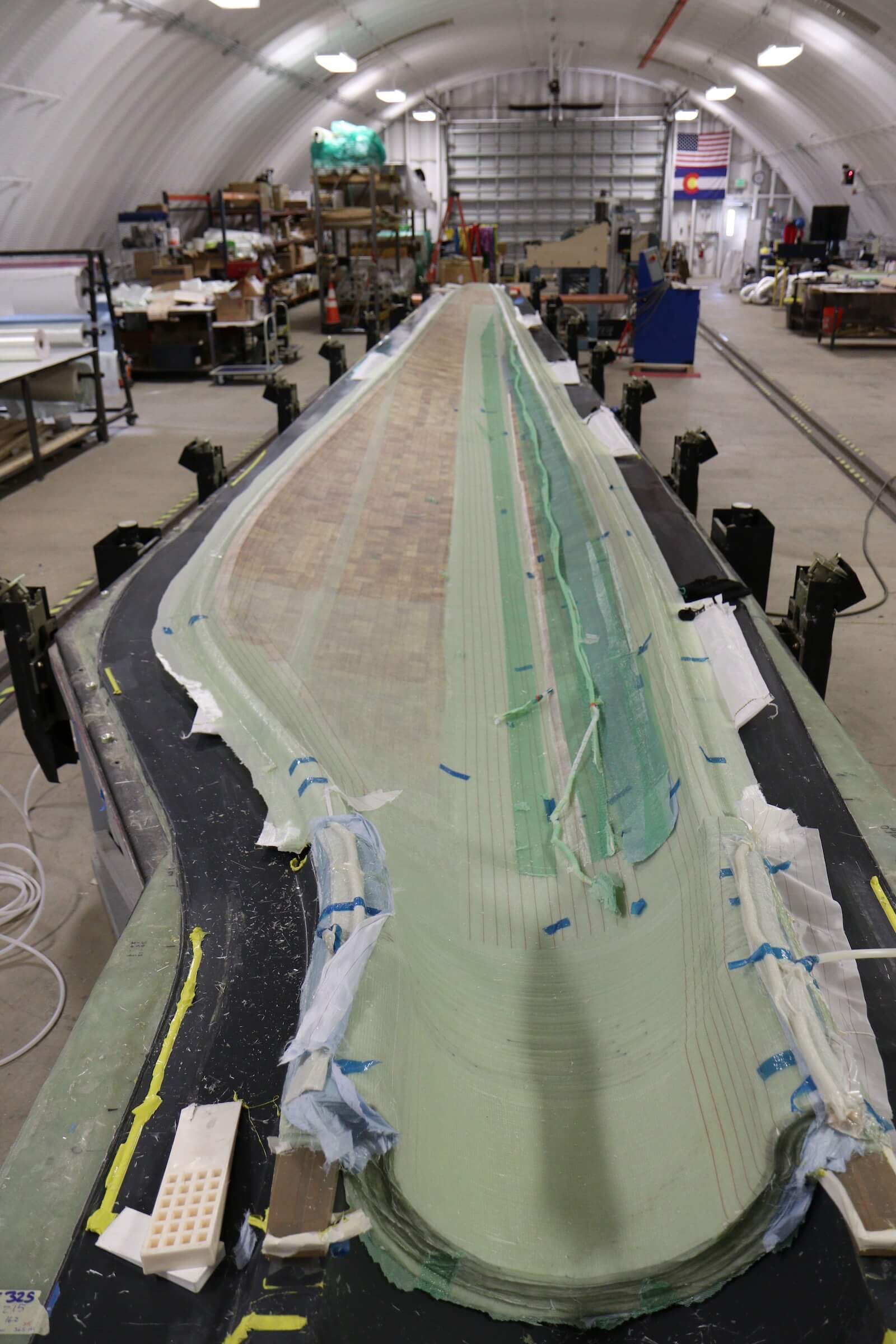
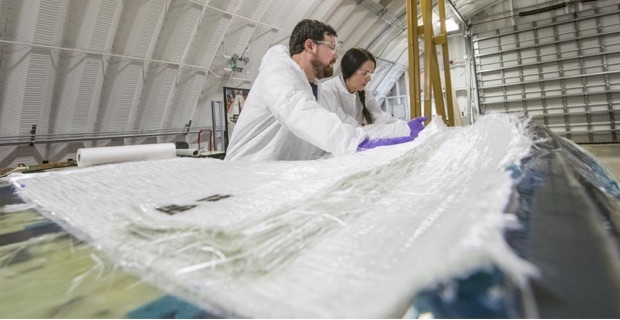
Figure 6 (left) and 7. Researchers at the National Renewable Energy Laboratory (NREL) construct a 13-m thermoplastic composite blade at NREL's Composites Manufacturing Education and Technology Facility. Photos by Ryan Beach, NREL
For instance, as part of its commitment to repurposing/recycling turbine blades, GE Renewable Energy agreed to partner with Veolia to establish a facility in Missouri that grinds wind turbine blades into materials that are used in the cement making process.[13] Similarly, the U.S. Department of Energy Wind Energy Technologies Office funded Carbon Rivers, LLC (a Knoxville, Tennessee, startup company that advances and commercializes a variety of technologies) to develop a thermal decomposition recycling process that allows the company to recover glass fibers from wind turbine blades, which can then be used in the manufacturing of new composite products.[14]
Repowering
Purpose
What is repowering and why is it done?
Repowering describes the retrofitting or replacement of wind turbines either in part (partial repowering) or in full (full repowering). It is a decision that is initiated by a project's owners and involves replacing older components with new technology rather than fully decommissioning (or removing) an existing wind energy project.
Full repowering activities are not common but will happen more frequently as projects reach the end of their lifetime. Partial repowering activities occur on a more frequent basis and have happened within the first 10 years of operation.[15]
Repowering allows the owner of an existing project to increase that project's energy production, extend project life on land that is already secured and sited, and/or access favorable tax incentives.[16]
Method
What does repowering entail?
A partial repower typically upgrades the blades, gearboxes, hubs, main shafts, main bearing assemblies, or other internal nacelle components with new technology while continuing to use the existing towers and foundations. In 2021, turbines involved in partial repowers ranged in age from 9 to 16 years old and had a median age of 10 years.[17]
These upgrades can result in a slight increase in nameplate capacity, or increase in total turbine height, and rotor diameter (see Figure 8) and are typically primarily intended to increase the capacity factor of each turbine and, thus, the energy output of the facility.
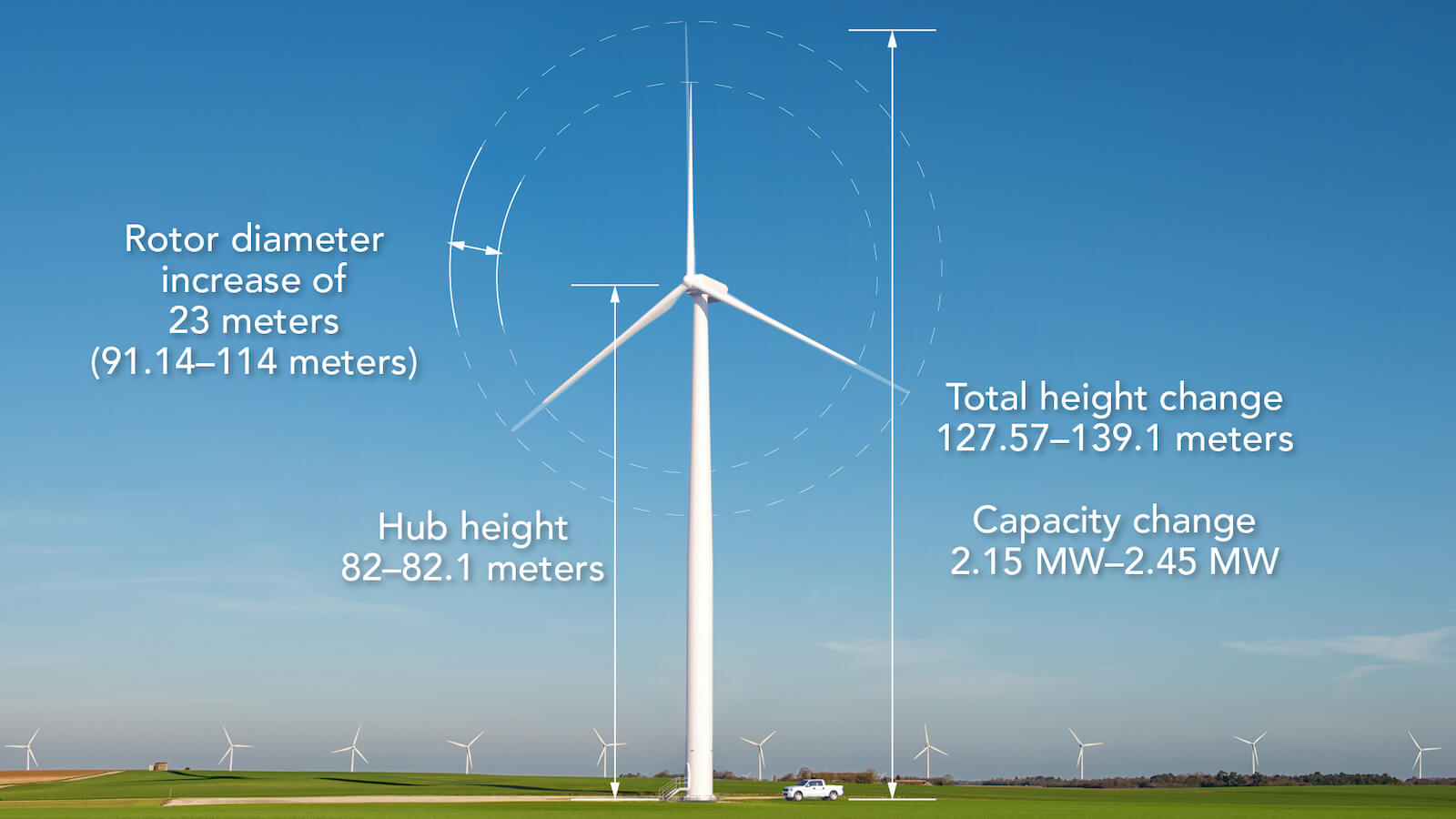
Figure 8. Based off statistics from the Land-Based Wind Market Report: 2022 Edition, this image highlights the potential differences in total wind turbine height and rotor diameter that can occur after a partial repower. In most cases, hub heights for partially repowered turbines will not change. Image by Josh Bauer, NREL
The extent of this impact is limited because partial repowers use existing towers and foundations that can only accommodate slight increases in component size. Still, a partial repowering may be subject to permit review and renewal under the current local zoning or other regulatory framework at the time of the repower.
Once the construction associated with a partial repower is complete, land restoration activities (i.e., reseeding, potential decompaction of construction and laydown areas, and/or replacing damaged drain tiles, etc.) are generally required to restore project sites to previous operating conditions.
A full repower is a far more extensive activity than a partial repower that typically involves the decommissioning of a wind energy project's original turbines and foundations, the construction of new wind turbines and foundations, and the replacement of associated electrical collection system, if needed.
With new towers and foundations, the turbines used in fully repowered projects are often significantly larger in overall size (turbine height and rotor diameter) and nameplate capacity than the original turbines they are replacing, allowing for changes to the overall capacity and/or layout of a project (see Figures 9 and 10). For instance, a fully repowered wind energy project could have the same number of turbines with a higher total capacity, or the project could have the same total capacity with fewer wind turbines. In 2020, three projects were fully repowered. In total, 343 turbines with a total capacity of 120 MW were replaced with 50 new turbines that had a total capacity of 148 MW.[18] No projects were fully repowered in 2021.[19]
Because a full repowering is typically a redesign of an existing wind energy project, the redesign will likely be subject to permit review and renewal under the current local zoning or other regulatory framework at the time of the repower. Project infrastructure (like access roads, substations, and collector lines) may also be removed, depending on whether these elements can be reused given the updated technology and project layout. Once the construction associated with a full repower is complete, restoration activities are generally required to reclaim and restore interrupted sites to pre-repower conditions.
Impact
What are the impacts of repowering?
Communities that are involved with repowering activities can experience a variety of impacts during the removal and new construction of wind turbine components and project-related infrastructure. This will include an influx of temporary workers who may spend time and money in the communities in and around the wind energy project, supporting the local economy. It may also provide an opportunity for local businesses and workers to provide construction support activities like land clearing, excavation, land restoration, trenching, or other project-focused efforts. Additional impacts from project construction (like increased noise and road wear) can also be expected because these activities will require the use of heavy equipment, component deliveries to and from the project, and increased project-related traffic. Repowering activities will also require the preparation of temporary component staging/laydown areas that can require significant amounts of land depending on project size and repowering type.
Full repowers generally require larger construction crews than partial repowers because of the additional complexity of these projects. A partial repower can be completed over a few months, whereas full repowers that include site restoration can take nearly 2 years to complete. All repowering timelines ultimately depend on the number of turbines being repowered.
In addition to the influx of workers, repowers can change the characteristics and layout of a wind energy project and could possibly alter other economic benefits for landowners and local governments, including land lease payments and project-related tax revenues. For example, wind energy projects can have fewer turbines, which can reduce the number of landowners who are directly compensated. However, depending on land leases and other agreements, increases in turbine capacity may lead to higher royalty payments for landowners. Additionally, repowering can be viewed as an opportunity for a community to work with project developers to sustain or increase project benefits to the community, like associated tax revenues, for the new life of the repowered project.
The larger turbines used in some repowers can alter how a project is experienced by those living near it. Larger turbines can be more visible to some residents, impacting local viewsheds and potentially changing shadow flicker at some homes that are near turbines. On the other hand, consolidating the layout with fewer, larger turbines may reduce the number of visible turbines and the number of homes that experience shadow flicker, which could be preferrable compared to having a larger number of smaller-capacity turbines.
Regardless of whether a repower is full or partial, these extension-of-life activities replace wind turbine components that must be processed and disposed of. Partial repowers are the primary reason blades are taken out of service prior to the anticipated operational lifetime of a wind turbine.[3] In 2021, 2,307 blades from 12 wind energy projects were retired due to partial repowering.[20]
Decommissioning
Purpose
What is decommissioning and when does it occur?
Decommissioning is the removal of a wind energy project (wind turbines and associated infrastructure) and the restoration of any land that was used as part of a wind energy project. Decommissioning typically occurs at the end of a wind energy project’s operational life or when a project is fully repowered. The development of a decommissioning plan is usually conducted as part of the original project development.
Method
How long does decommissioning take? And what are the activities that make up decommissioning?
The time to disassemble, demolish, and remove wind turbine components (see Figure 12) and wind energy project-related infrastructure and conduct restoration activities can be 6–24 months, depending on the size of the turbines and the number of turbines involved in the project.
Some project infrastructure, like overhead lines, underground lines, and substations, may be reused when decommissioned turbines are removed and replaced during a full repowering. If located on privately owned land, access roads may be kept at the discretion of the landowner.
Land lease agreements and local ordinances often include language that ensures sites are restored as closely as practical to pre-project conditions after turbines and related infrastructure are removed. This can include decompacting land, reseeding vegetation, and replacing any damaged drainage tiles.
Although a wind energy project owner may be required to remove nearly all above-ground infrastructure (e.g., substations, wires, buildings, fencing, and access roads) and restore the land to agreed-upon conditions, many communities choose to define a removal depth that allows some below-ground infrastructure (e.g., foundation and wiring) to remain in place due to environmental impacts associated with complete removal. Environmental impacts during decommissioning/full removal of below-ground infrastructure can include noise disturbances, ground disturbance, and more. Additional environmental concerns related to full foundation removal may include compromised site stability, erosion, or unwanted pathways for surface and sub-surface water due to inappropriate backfilling of the site.[21] Although partially leaving a foundation in place can limit some environmental impacts, the remaining infrastructure may have its own potential impacts, such as impairing drainage or creating new pathways for water. The agreed-upon depth should be deep enough to ensure that the remaining infrastructure does not interfere with future land use, including agriculture (see Figure 11). The amount of topsoil used for backfilling a site will depend on land use and geographic location.
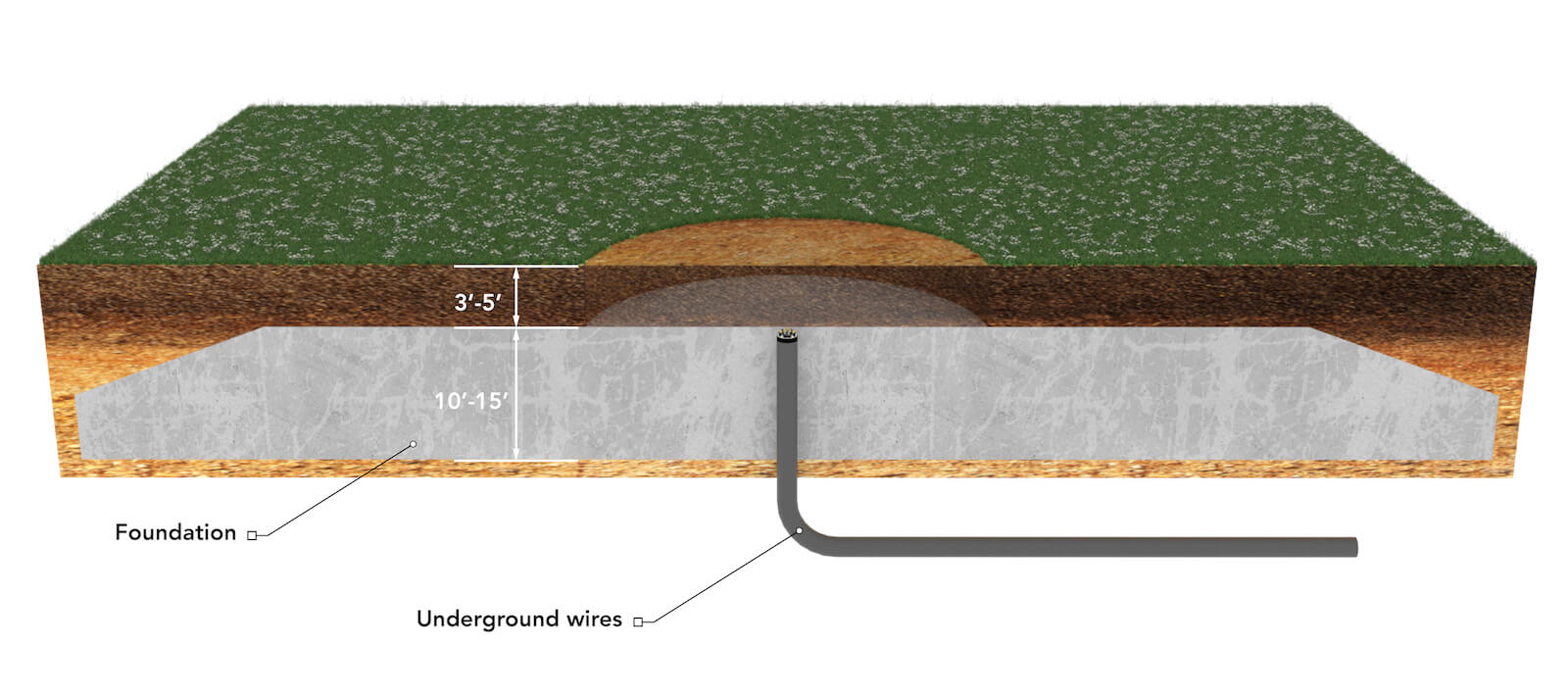
Figure 11. The below ground infrastructure for a wind turbine includes the foundation and underground wires. Foundations can have a 32-foot radius and a depth of 20 feet. Decommissioning standards at the state or local level determine the removal depth for these project components. Most decommissioning standards allow in-ground components below 3-5 feet to remain in place. Image by Josh Bauer, NREL
Cost
How much does it cost to decommission a turbine or a project? And who pays for it?
Wind energy project decommissioning costs depend on project location and labor rates, turbine size (larger turbines have higher decommissioning costs), transportation costs, total number of turbines, and salvage rates per ton for materials like steel, aluminum, and copper.
Decommissioning estimates from third-party contractors are often required during the permitting process and many state and local regulations establish standards that ensure these estimates are updated throughout the lifetime of a project.
Data from a limited review of eight decommissioning estimates for wind energy projects proposed in 2019–2021 showed per-turbine decommissioning costs (total decommissioning costs divided by number of turbines) of $114,000–$195,000. When salvage estimates were included, decommissioning costs were reduced to a net range of $67,000–$150,000 per turbine.[22]
Jurisdictional (federal, state, or local) authority for decommissioning depends on project location and land control. In nearly all cases, project owners are responsible for the cost of wind turbine disassembly, off-site disposal, site restoration, and/or recycling of project-related components and materials. In addition to requirements from federal, state, or local authorities, lease contracts also typically hold project owners responsible for costs related to disassembling, transporting, disposing, and restoring wind energy projects and project sites. This provides landowners with additional legal recourse if the project owner does not decommission the turbine on their property.
To ensure that funds will be available to decommission a project at the end of its operational lifetime, state regulations or local ordinances might require project developers or owners to post some form of financial assurance (i.e., a bond, self-guarantee, parent-company guarantee, or letter of credit), which will be held until the project is successfully decommissioned. These will be released once decommissioning is completed to the standards designated in the wind energy ordinance, decommissioning plan, land lease agreement, and/or other applicable regulations. In some cases, financial assurance is not required until the project has been operational for a length of time previously defined by local decision makers and project developers or owners because requiring financial assurance up front can be cost prohibitive to developers.
The decommissioning of a wind energy project may also have local economic impacts caused by the loss of operations and maintenance jobs, land lease payments, property tax payments, and other forms revenue generation.
Blades
Waste
How does blade waste compare to other waste?
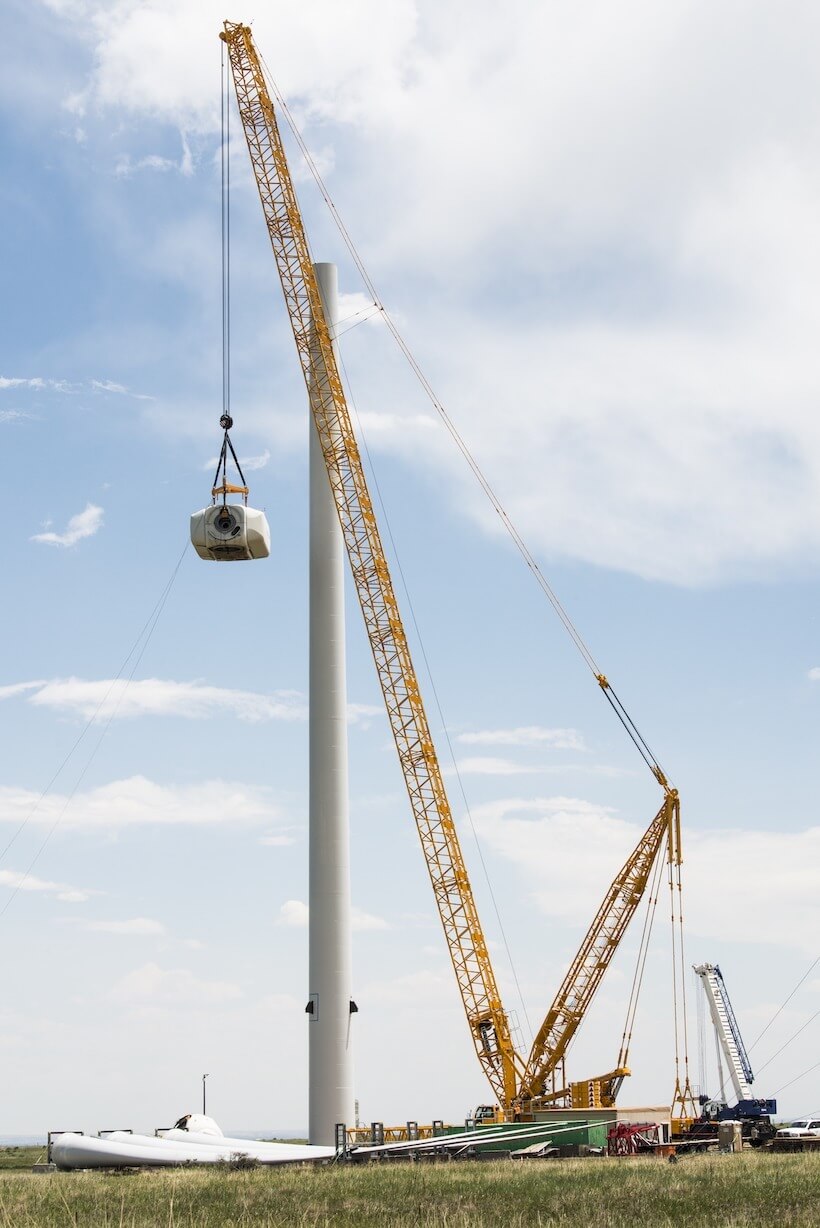
Figure 12. Crews lower the nacelle as part of the decommissioning of the 3-MW Alstom wind turbine at NREL’s National Wind Technology Center. Photo by Dennis Schroeder. NREL 51733
Because landfilling remains the most cost-effective option to process blades and other composite components (as of 2022), it is important to understand waste in the United States and how much wind energy contributes to that larger picture.[23] In 2018, about 146.1 million tons of municipal solid waste[25] and 145 million tons of construction and demolition waste[3] were managed at U.S. landfills.
Estimates related to the amount of decommissioned wind energy blades have shown that less than 50,000 tons of blade waste, equivalent to 0.017% of combined municipal solid waste and construction and demolition waste, were managed by landfills in 2018.
By 2050, it is projected that wind turbine blade waste could range from about 200,000 to 370,000 tons per year, depending on operational lifetime of these components (15–25 years).[26] Even at this level, blade waste would be equivalent to less than 0.15% of combined municipal solid waste and construction and demolition waste from 2018. Landfilled wind turbine blades and other composite components are not considered hazardous waste.[27],[28]
An additional blade disposal/processing concern for some communities pertains to the amount of space taken up by turbine blades due to their size. The amount of space needed depends on how the blade is segmented and if it is further crushed, shredded, or otherwise processed. Some communities have limited landfill space that can prohibit their ability to accept and process these components.
Quantity
How many blades are taken out of service annually?
In 2021, 2,307 blades from 12 wind energy projects were taken out of service due to partial repowering.[29]
The average rate of retirements is expected to be 3,000–9,000 blades per year for 2021–2026, increasing to 10,000–20,000 per year by 2040 as old technology is repowered and/or projects/components reach the end of their operational lives (see Figure 13).[30]
As of July 2022, there are 72,130 turbines with more than 210,000 blades deployed across the country.[1]
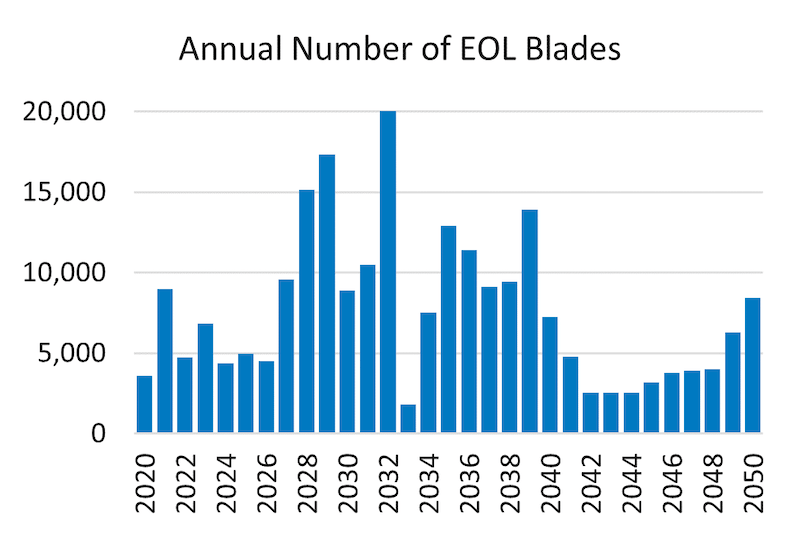
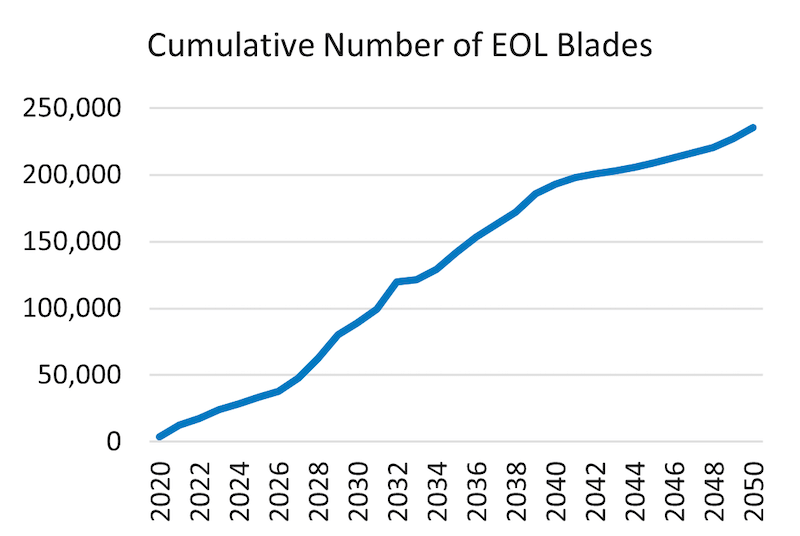
Figure 13. Estimates of end-of-life (EOL) wind turbine blades taken out of service each year (left) and total (right). Image from Cooperman, Eberle, and Lantz.
Recyclability
Why have blades been difficult to recycle?
Wind turbine blades are made from composite materials that are designed to be strong, lightweight, and durable so that they can operate consistently for long periods of time without deteriorating. Blades (alongside other composite components, like nacelle covers and rotor covers) make up approximately 6%–14% of a wind turbine’s mass.[31],[32] While a vast majority of a wind turbine is easily recyclable, composite components have been difficult to process and, until the last 3 years, there were limited viable options outside of landfilling to process these products domestically.
Though recycling and repurposing methods have been introduced into the U.S. market, most wind turbine blades are currently disposed of in landfills due to the current limited availability and higher cost of these methods. The total number of blades that are recycled or repurposed each year compared to the total number of blades that are landfilled is difficult to determine, but as of 2022, blade recyclers in the United States have the capacity to recycle more than 3,000 blades per year.[33]
As new end-of-service processing methods mature and secondary supply chains are developed, opportunities for wind turbine blade recycling and repurposing are expected to become more widely available. Additionally, as recycling costs decrease, these alternatives will become economically competitive with landfilling, resulting in a higher percentage of turbine blades having secondary lives as materials that can be used in the manufacturing of new products.
Alternatives
What options are currently available to avoid the landfilling of blades? And what will be available in the future?
Alternatives to landfilling of wind turbine blades and other composite components that have been introduced into the United States include mechanical recycling, thermal decomposition recycling, and repurposing:
- Mechanical recycling is a process that grinds or shreds blades into materials that are repurposed for use in other manufacturing processes as replacement material within a product (like concrete) and/or replacement fuel to make a product (like coal used in concrete kilns).
- Thermal decomposition recycling is a process that uses heat to recover glass fibers that can then be upcycled into new composite-based products.
- Repurposing involves the direct use of the decommissioned component—in this case, wind turbine blades—to create new products, like pedestrian bridges, playgrounds, benches, bike shelters, affordable housing, and noise barriers (see Figure 14).
Research is currently being conducted to develop wind turbine blades that are specifically designed to be recycled. In fact, multiple OEMs have prototypes of recyclable blades that have already been manufactured and are currently undergoing testing to determine overall performance (see Figure 15).[34]
Some next-generation recyclable blades may feature a new manufacturing process that replaces thermoset epoxy resin, which is currently used to make wind turbine blades, with a thermoplastic resin that allows for more complete and economically viable recycling of these components.
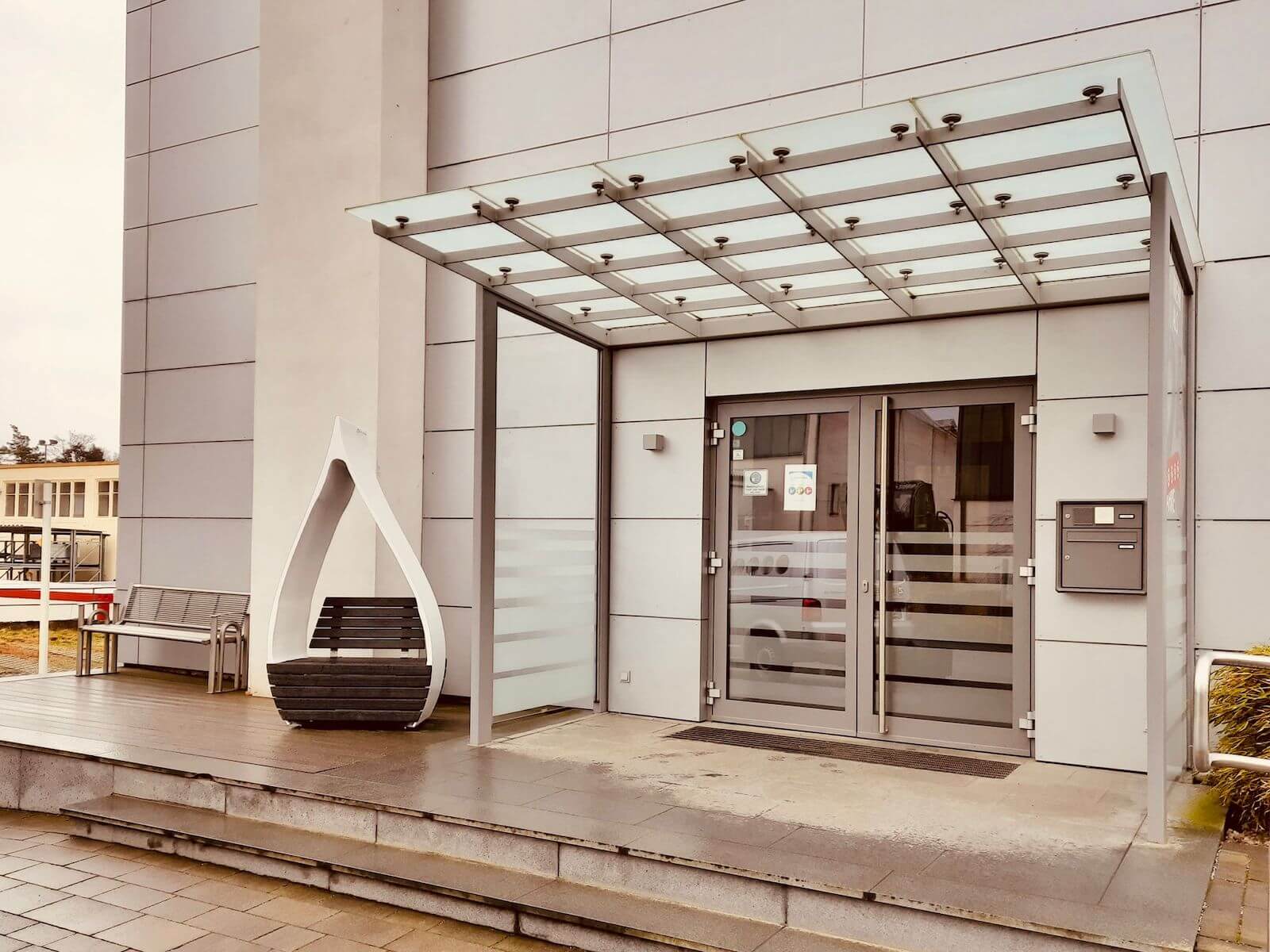
Figure 14. Wind turbine blades can be repurposed into a wide variety of applications. The example shows a repurposed blade that has been used to create outdoor seating. Photo from Anmet
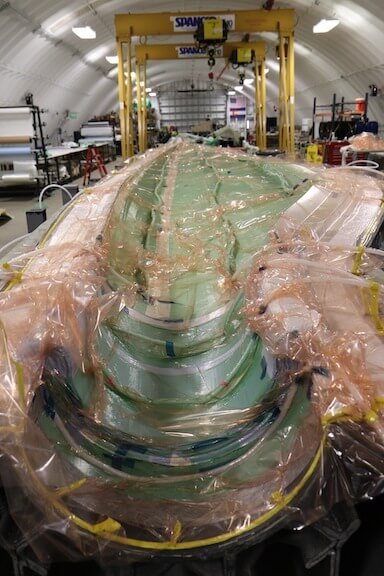
Figure 15. Construction of a revolutionary 13-meter thermoplastic blade at NREL's Composites Manufacturing Education and Technology Facility. A vacuum bag covers the laminate and mold, which is infused with resin. This blade is specifically designed to be recycled at the end of its service. Photo by Ryan Beach, NREL 62034
Works Cited
[1] Hoen, B.D., J.E. Diffendorfer, J.T. Rand, L.A. Kramer, C.P. Garrity, and H.E. Hunt. 2018. “United States Wind Turbine Database v5.0.” October 12, 2022. U.S. Geological Survey, American Clean Power Association, and Lawrence Berkeley National Laboratory. https://doi.org/10.5066/F7TX3DN0. (See https://eerscmap.usgs.gov/uswtdb/viewer/#3/37.25/-96.25.)
[2] Woods Mackenzie North American Wind Energy Market Outlook 2022
[3] Wiser, R. and M. Bolinger. 2019. Benchmarking Anticipated Wind Project Lifetimes: Results from a Survey of U.S. Wind Industry Professionals. Berkeley, CA: Lawrence Berkeley National Laboratory. https://emp.lbl.gov/publications/benchmarking-anticipated-wind-project.
[4] GE Renewable Energy. 2020. “GE Renewable Energy Announces US Blade Recycling Contract with Veolia.” Press Release. December 8, 2020. https://www.ge.com/news/press-releases/ge-renewable-energy-announces-us-blade-recycling-contract-with-veolia
[5] Farzan, S. 2022. “How to Recycle a 150-Foot Wind Turbine Blade? Haul It to Louisiana, MO.” St. Louis Public Radio. May 27, 2022. https://news.stlpublicradio.org/health-science-environment/2022-05-27/how-to-recycle-a-150-foot-wind-turbine-blade-haul-it-to-louisiana-mo.
[6] Pehlken, Alexandra & Garcia Sanchez, Rosa. (2013). “How Critical Is Wind Energy?” In Sustainable Material Life Cycles - Is Wind Energy really Sustainable? Hanse Studies Volume 9. Edited by Alexandra Pehlken, Andreas Solsbach, Wolfgang Stenzel, 85–102. Oldenburg, Germany: BIS-Verlag der Carl von Ossietzky Universtät Oldenburg. https://www.researchgate.net/publication/280529029_How_critical_is_wind_energy.
[7] Vestas. 2020. The Vestas Sustainability Report 2019. Aarhus N., Denmark: Vestas Wind Systems A/S. https://www.vestas.com/en/sustainability/reports-and-ratings#lcadownload.
[8] Tota-Maharaj, K. and A. McMahon. 2021. Resource and Waste Quantification Scenarios for Wind Turbine Decommissioning in the United Kingdom. Waste Disposal and Sustainable Energy 3: 117–144. https://doi.org/10.1007/s42768-020-00057-6.
[9] García Sánchez, R. and A. Pehlken, and M. Lewandowski. 2014. On the Sustainability of Wind Energy Regarding Material Usage. University Politehnica Timisoara. Acta Tehnica Corvinieses – Bulletin of Engineering VII (January–March). https://www.researchgate.net/publication/262672882_ON_THE_SUSTAINABILITY_OF_WIND_ENERGY_REGARDING_MATERIAL_USAGE.
[10] Carrara, S., Alves Dias, P., Plazzotta, B. and Pavel, C. 2020. Raw Materials Demand for Wind and Solar PV Technologies in the Transition Towards a Decarbonised Energy System. Luxembourg, Luxembourg: Publications Office of the European Union. EUR 30095 EN JRC119941. https://publications.jrc.ec.europa.eu/repository/handle/JRC119941
[11] Welstead, J., Hirst, R., Keogh, D., Robb G. and Bainsfair, R. 2013. Research and guidance on restoration and decommissioning of onshore wind farms. Scottish Natural Heritage Commissioned Report No. 591. https://citeseerx.ist.psu.edu/viewdoc/download?doi=10.1.1.397.2847&rep=rep1&type=pdf
[12] National Renewable Energy Laboratory. “News Release: NREL Advanced Manufacturing Research Moves Wind Turbine Blades Toward Recyclability.” National Renewable Energy Laboratory. Nov. 17, 2020. https://www.nrel.gov/news/press/2020/nrel-advanced-manufacturing-research-moves-wind-turbine-blades-toward-recyclability.html.
[13] General Electric. 2020. “GE Renewable Energy Announces US Blade Recycling Contract With Veolia.” General Electric News. Dec. 8, 2020. https://www.ge.com/news/press-releases/ge-renewable-energy-announces-us-blade-recycling-contract-with-veolia.
[14] U.S. Department of Energy Wind Energy Technologies Office. 2021. “No Time To Waste: A Circular Economy Strategy for Wind Energy.” Spring 2021 R&D Newsletter. June 2, 2021. https://www.energy.gov/eere/wind/articles/no-time-waste-circular-economy-strategy-wind-energy.
[15] Wiser, R., Bolinger, M., Hoen, B., Millstein, D., Rand, J., Barbose, G., Darghouth, N., Gorman, W., Jeong, S., and Paulos, B. Land-Based Wind Market Report: 2022 Edition. Oak Ridge, Tennessee: U.S. Department of Energy. https://www.energy.gov/sites/default/files/2022-08/land_based_wind_market_report_2202.pdf.
[16] Wiser, R., Bolinger, M., Hoen, B., Millstein, D., Rand, J., Barbose, G., Darghouth, N., Gorman, W., Jeong, S., and Paulos, B. Land-Based Wind Market Report: 2022 Edition. Oak Ridge, Tennessee: U.S. Department of Energy. https://www.energy.gov/sites/default/files/2022-08/land_based_wind_market_report_2202.pdf
[17] Wiser, R., Bolinger, M., Hoen, B., Millstein, D., Rand, J., Barbose, G., Darghouth, N., Gorman, W., Jeong, S., and Paulos, B. Land-Based Wind Market Report: 2022 Edition. Oak Ridge, Tennessee: U.S. Department of Energy. https://www.energy.gov/sites/default/files/2022-08/land_based_wind_market_report_2202.pdf
[18] Wiser, Ryan H., M. Bolinger, B. Hoen, D. Millstein, J. Rand, G.L. Barbose, N.R. Darghouth, W. Gorman, S. Jeong, A.D. Mills, and B. Paulos. 2021. Land-Based Wind Market Report: 2021 Edition. Oak Ridge, Tennessee: U.S. Department of Energy. DOE/GO-102021-5611. https://emp.lbl.gov/sites/default/files/land-based_wind_market_report_2021_edition_final.pdf.
[19] Wiser, R., Bolinger, M., Hoen, B., Millstein, D., Rand, J., Barbose, G., Darghouth, N., Gorman, W., Jeong, S., and Paulos, B. Land-Based Wind Market Report: 2022 Edition. Oak Ridge, Tennessee: U.S. Department of Energy. https://www.energy.gov/sites/default/files/2022-08/land_based_wind_market_report_2202.pdf
[20] Wiser, R., Bolinger, M., Hoen, B., Millstein, D., Rand, J., Barbose, G., Darghouth, N., Gorman, W., Jeong, S., and Paulos, B. Land-Based Wind Market Report: 2022 Edition. Oak Ridge, Tennessee: U.S. Department of Energy. https://www.energy.gov/sites/default/files/2022-08/land_based_wind_market_report_2202.pdf.
[21] Welstead, J., Hirst, R., Keogh, D., Robb G. and Bainsfair, R. 2013. Research and guidance on restoration and decommissioning of onshore wind farms. Scottish Natural Heritage Commissioned Report No. 591. https://citeseerx.ist.psu.edu/viewdoc/download?doi=10.1.1.397.2847&rep=rep1&type=pdf
[22] Decommissioning plans, siting applications from the following wind energy projects were used to determine the range of decommissioning costs per turbine and decommissioning costs minus salvage per turbine. Lincoln Land Wind Project, Buffalo Ridge Wind Energy Center, Great Pathfinder Wind
, PrairieWinds SD 1
, Rail Tie Wind
, Plum Creek Wind Project, Canisteo Wind, and Walleye Wind.
[23] Cooperman, A., A. Eberle, and E. Lantz. 2021. Wind Turbine Blade Material in the United States: Quanitites, Costs, and End-of-Life Options. Resources, Conservation and Recycling 18: 105439. https://doi.org/10.1016/j.resconrec.2021.105439.
[24] United States Environmental Protection Agency. 2021. “National Overview: Facts and Figures on Materials, Wastes and Recycling.” Last updated July 14, 2021. https://www.epa.gov/facts-and-figures-about-materials-waste-and-recycling/national-overview-facts-and-figures-materials
[25] United States Environmental Protection Agency. 2021. “Sustainable Management of Construction and Demolition Materials.” Last updated May 18, 2021. https://www.epa.gov/smm/sustainable-management-construction-and-demolition-materials.
[26] Electric Power Research Institute. 2020. Wind Turbine Blade Recycling: Preliminary Assessement. Palo Alto, CA: Electric Power Research Institute. 3002017711. https://www.epri.com/research/products/000000003002017711.
[27] Beauson, J., A. Laurent, D.P. Rudolph, and J. Pagh Jensen. 2022. The Complex End-of-Life of Wind Turbine Blades: A Review of the European Context. Renewable and Sustainable Energy Reviews 155: 111847. https://doi.org/10.1016/j.rser.2021.111847. https://www.sciencedirect.com/science/article/pii/S136403212101114X
[28] North Carolina Department of Environmental Quality Environmental Management Commission. 2021. Final Report on the Activities Conducted to Establish a Regulatory Program for the Management and Decommissioning of Renewable Energy Equipment. Raleigh, NC: North Carolina Environmental Quality. HB329 Final Report. https://deq.nc.gov/h329-final-report.
[29] Wiser, R., Bolinger, M., Hoen, B., Millstein, D., Rand, J., Barbose, G., Darghouth, N., Gorman, W., Jeong, S., and Paulos, B. Land-Based Wind Market Report: 2022 Edition. Oak Ridge, Tennessee: U.S. Department of Energy. https://www.energy.gov/sites/default/files/2022-08/land_based_wind_market_report_2202.pdf.
[30] Cooperman, A., A. Eberle, and E. Lantz. 2021. Wind Turbine Blade Material in the United States: Quanitites, Costs, and End-of-Life Options. Resources, Conservation and Recycling 18: 105439. https://doi.org/10.1016/j.resconrec.2021.105439.
[31] Tota-Maharaj, K. and A. McMahon. 2021. Resource and Waste Quantification Scenarios for Wind Turbine Decommissioning in the United Kingdom. Waste Disposal and Sustainable Energy 3: 117–144. https://doi.org/10.1007/s42768-020-00057-6
[32] García Sánchez, R. and A. Pehlken, and M. Lewandowski. 2014. On the Sustainability of Wind Energy Regarding Material Usage. University Politehnica Timisoara. Acta Tehnica Corvinieses – Bulletin of Engineering VII (January–March). https://www.researchgate.net/publication/262672882_ON_THE_SUSTAINABILITY_OF_WIND_ENERGY_REGARDING_MATERIAL_USAGE
[33] Farzan, S. 2022. “How to Recycle a 150-Foot Wind Turbine Blade? Haul It to Louisiana, MO.” St. Louis Public Radio. May 27, 2022. https://news.stlpublicradio.org/health-science-environment/2022-05-27/how-to-recycle-a-150-foot-wind-turbine-blade-haul-it-to-louisiana-mo.
[34] General Electric. 2022. "ZEBRA Blade Achieves Key Milestone With Production of the First Prototype of Its Recyclable Wind Turbine Blade.” General Electric. March 17, 2022. https://www.ge.com/news/press-releases/zebra-project-achieves-key-milestone-with-production-of-first-prototype-of-recyclable-wind-turbine-blade.