Table of Contents
- Introduction
- Array Cables
- Blades
- Export Cables
- Monopiles
- Nacelles
- Towers
- Transition Pieces
- References
- Publication Information
See additional WINDExchange guides and resources to learn about offshore wind energy workforce safety standards and training and development best practices.
By Caitlyn Clark, Brinn McDowell, Bailey Pons, Jeremy Stefek at the National Renewable Energy Laboratory for the U.S. Department of Energy Wind Energy Technologies Office
Introduction
The job opportunity for component manufacturing facilities and their suppliers could be a significant portion of the offshore wind energy workforce (see the U.S. Department of Energy’s wind energy career map). Average annual employment levels (full-time equivalent [FTE]/year) from 2024 to 2030 are estimated at 12,300 and 49,000 based on 25% and 100% domestic content scenarios, respectively, to fabricate and assemble components to reach 30 gigawatts (GW) of offshore wind energy by 2030.[1] The extent to which domestic jobs are realized depends on the building of U.S. manufacturing facilities and those facilities leveraging a U.S. supply chain to source subassemblies, parts, and materials.
In recent years, researchers at the U.S. Department of Energy’s National Renewable Energy Laboratory have conducted a research effort, supported by the Wind Energy Technologies Office, to better understand the job needs for major component manufacturing facilities (e.g., Tier 1 facilities). Many useful insights have been shared in different reports, including:
- Offshore Wind Energy Workforce Assessment (Stefek, 2022)
[2]
- The Demand for a Domestic Offshore Wind Energy Supply Chain (Shields, 2022)
[3]
- A Supply Chain Road Map for Offshore Wind Energy in the United States (Shields, 2023)
.[4]
This resource compiles insights from these reports to estimate the number of workers within facilities, list roles and certifications, and show the magnitude of supplier job opportunities for each major component, including:
Return to topArray Cables
The figure below shows the estimated number of direct jobs in the major component manufacturing facility based on the number of workers needed, and facilities opening over time to fabricate components to reach a target of 30 GW of offshore wind by 2030. The jobs count below represents any person working in a facility who produces or oversees the fabrication and assembly of the component, including tradespeople, managers, engineers, and professional service performers.
The number of FTEs available is based on the number of direct FTE per facility multiplied by the number of facilities to produce supply 4–6 GW of projects per year. Direct FTEs are estimated from interviews and surveys of facility operators.
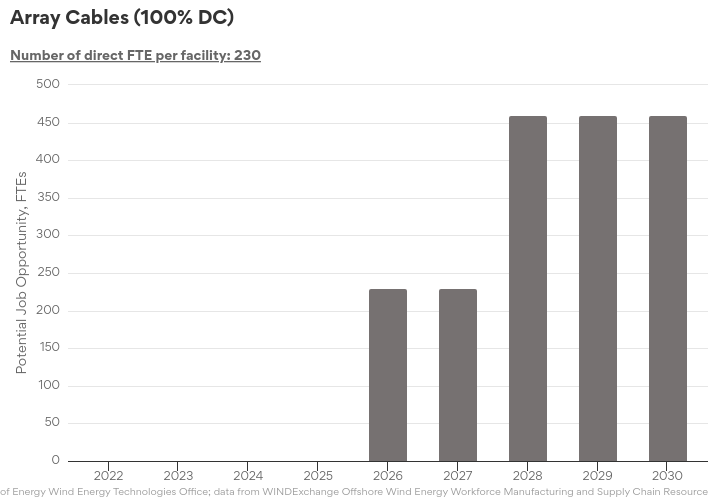
The workers in each major component facility include different types of roles with various levels of education and experience requirements. The table below shows four different workforce categories and lists the types of occupations that exist to fabricate and assemble the major component, listed in alphabetical order by name.
Table 1. Array Cable Roles
Responsibility Level |
Job Positions |
---|---|
Factory-Level Management |
|
Design and Engineering |
|
Quality and Safety |
|
Factory-Level Work |
|
The employees fabricating a component may have to complete a workforce certification based on the scope of work. Certification needs specific to the component are listed in the table below in alphabetical order by name. Additional research is needed to align the certifications with a specific occupation and understand the training needs for certifications.
Table 2. Array Cable Job Certifications
Certification |
Length of Time |
Resource |
---|---|---|
Certified Manager of Quality/Organizational Excellence (CMQ/QE) |
10-15 years |
|
Certified Quality Improvement Associate (CQIA) |
2 years |
|
Certified Quality Process Analyst (CQPA) |
2 years |
|
Certified Reliability Engineer (CRE) |
11 years |
|
Certified Quality Technician (CQT) |
4 years |
|
Certified Quality Technician (CQT) |
4 years |
|
Certified Welding Inspector (CWI) |
2-8 weeks |
|
Computer Numerical Control (CNC) Lathe Operations |
37 hours |
|
Computer Numerical Control (CNC) Lathe Programming Setup and Operations |
Varies by program |
|
Computer numerical control (CNC)Mill Operation |
38 hours |
|
Global Wind Organization Basic Safety Training (GWO BST) |
2 days |
https://www.globalwindsafety.org/standards/basic-safety-training-standard |
ICS: 29.020 Electrical Engineering |
Varies by program |
|
ISO 9001: 2015 Certified Lead Auditor |
2 weeks |
https://asq.org/training/iso-9001-2015-certified-lead-auditor-viso90012015cla |
Lean Certification |
8–16 weeks |
|
Milling I |
Less than a year |
|
National Commission for the Certification of Crane Operators (NCCCO) |
1 year |
https://www.nccco.org/nccco/certifications/tower-crane-operator/certification-overview |
Nondestructive Testing (NDT) |
8 months |
|
OSHA 10 |
2 days |
|
OSHA 30 |
4 days |
|
Six Sigma Green Belt Certification |
10 weeks |
https://www.sixsigmacouncil.org/six-sigma-green-belt-certification/ |
Jobs within the supply chain could be the largest contributor of employment in the offshore wind industry across all job sectors. For every job created in major component manufacturing facilities, there is an opportunity space to train and hire up to five supplier jobs to produce subassemblies, parts, and materials. In addition, workers with relevant skills and capabilities at existing businesses across the country participate in the offshore wind supply chain. The number of supplier jobs will depend on the level of domestic content in the supporting supply chain, with the numbers below assuming 25% to 100% domestic content (i.e., how many of these products are made in the United States instead of being imported). The figure below maps component-by-component flowcharts with a breakdown of workforce magnitude for each subassembly or subcomponent.
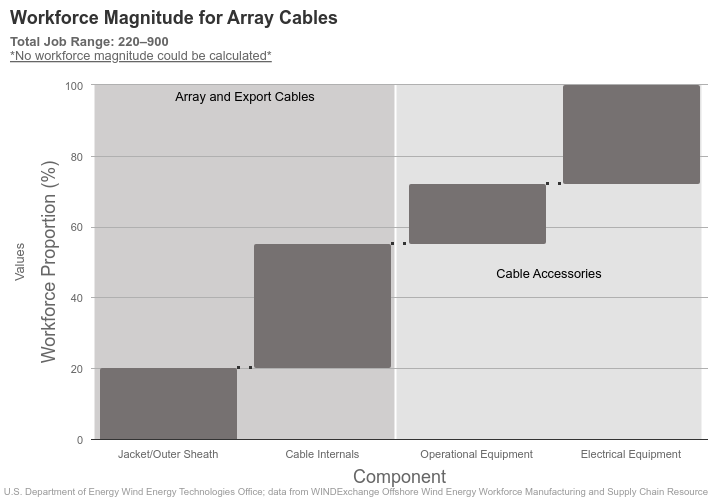
Blades
The figure below estimates the direct job needs in the major component manufacturing facility based on the number of workers needed, and facilities opening over time to fabricate components to reach a 30 GW by 2030 target. The jobs count below represent any person working in the facility to produce or oversee the fabrication and assembly, including tradespeople, managers, engineers, and professional services.
The number of FTEs available is based on the number of direct FTE per facility multiplied by the number of facilities to produce supply 4–6 GW of projects per year. Direct FTEs are estimated from interviews and surveys of facility operators.
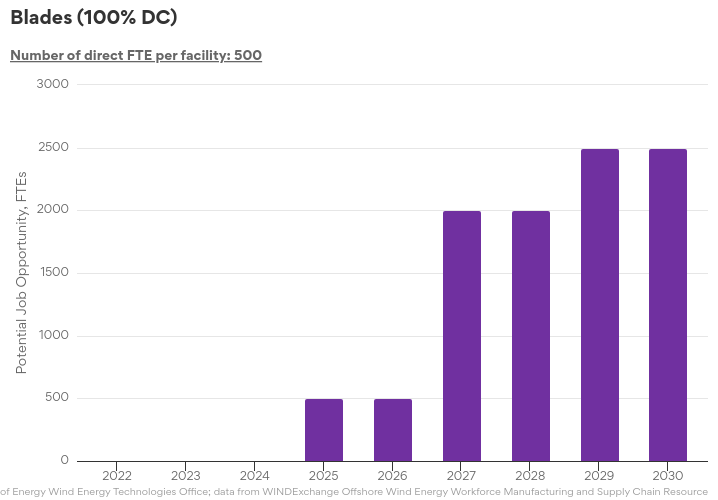
The workers in each major component facility include different types of roles with various levels of education and experience requirements. The table below shows four different workforce categories and lists the types of occupations that exist to fabricate and assemble the major component, listed in alphabetical order by name.
Table 1. Blade Roles
Responsibility Level |
Job Positions |
---|---|
Factory-Level Management |
|
Design and Engineering |
|
Quality and Safety |
|
Factory-Level Work |
|
The employees fabricating a component may have to complete a workforce certification based on the scope of work. Certification needs specific to the component are listed in the table below in alphabetical order by name. Additional research is needed to align the certifications with a specific occupation and understand the training needs for certifications.
Table 2. Blade Job Certifications
Certification |
Length of Time |
Resource |
---|---|---|
API 577: Welding Inspection and Metallurgy |
1-5 years |
|
ASME Practical Welding Technology |
8 Days |
|
Certified Calibration Technician (CCT) |
5 years |
|
Certified Coating Applicator (CCA) |
4 years |
|
Certified Quality Inspector (CQI) |
2 years |
|
Certified Welding Inspector (CWI) |
2-8 weeks |
|
Computer numerical control (CNC)Lathe Operations |
37 hours |
|
Computer numerical control (CNC)Lathe Programming Setup and Operations |
Varies by program |
|
Computer numerical control (CNC)Mill Operation |
38 hours |
|
Drill Rig Operator National Commission for the Certification of Crane Operator |
4–10 years |
https://www.nccco.org/nccco/certifications/drill-rig-operator |
Global Wind Organization Basic Safety Training (GWO BST) |
2 days |
https://www.globalwindsafety.org/standards/basic-safety-training-standard |
ISO/AWI 15513: Cranes |
Varies by program |
|
Milling I |
Less than a year |
|
National Association of Manufacturers |
Varies by program |
https://www.nam.org/legal-expertise/manufacturing-institute/ |
National Commission for the Certification of Crane Operators (NCCCO) |
1 year |
https://www.nccco.org/nccco/certifications/tower-crane-operator/certification-overview |
National Institute for Metalworking Skills |
Varies by program |
|
National Occupational Competency Testing Institute |
Varies by program |
|
Nondestructive Testing (NDT) |
8 months |
|
OSHA 10 |
2 days |
|
OSHA 30 |
4 days |
|
OSMRE Blaster Certification |
3 years |
https://www.osmre.gov/sites/default/files/inline-files/OSM%2074%20exp%202024%20update%206.17.21.pdf |
Surface Mount Technology Association (SMTA) |
1.5 days |
Supplier jobs represent the greater job market opportunity in the offshore wind workforce across all sectors. For every job created in these major component manufacturing facilities, there is an opportunity space to train and hire up to five supplier jobs to produce subassemblies, parts, and materials. In addition, existing businesses with relevant skills and capabilities across the country participate in the offshore wind supply chain. The number of supplier jobs will depend on the level of domestic content in the supporting supply chain, with the numbers below assuming 25% to 100% domestic content (i.e., how many of these products are made in the United States instead of being imported). The figure below maps component-by-component flowcharts with a breakdown of workforce magnitude for each subassembly or subcomponent.
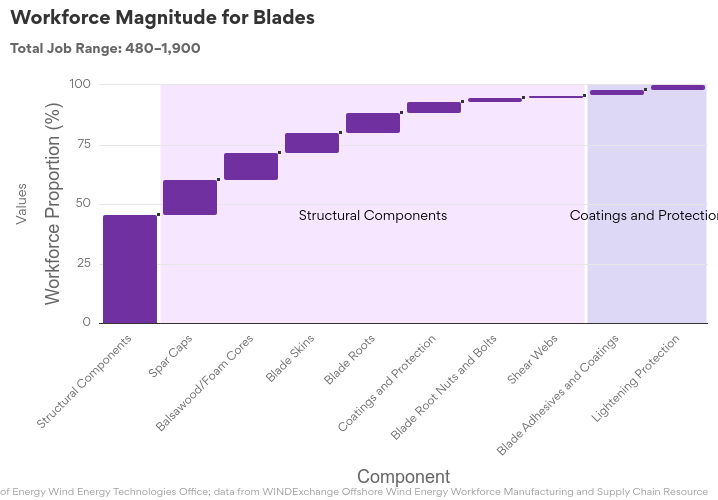
Export Cables
The figure below estimates the direct job needs in the major component manufacturing facility based on the number of workers needed, and facilities opening over time to fabricate components to reach a 30 GW by 2030 target. The jobs count below represents any person working in the facility to produce or oversee the fabrication and assembly, including tradespeople, managers, engineers, and professional services.
The number of FTEs available is based on the number of direct FTE per facility multiplied by the number of facilities to produce supply 4–6 GW of projects per year. Direct FTEs are estimated from interviews and surveys of facility operators.
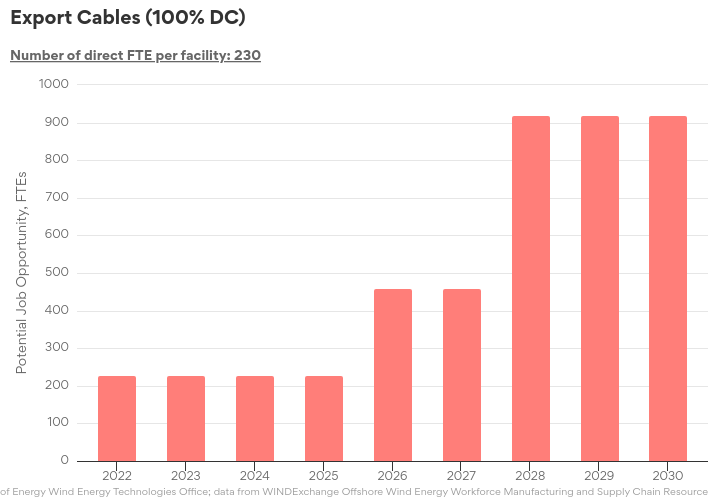
The workers in each major component facility include different types of roles with various levels of education and experience requirements. The table below shows four different workforce categories and lists the types of occupations that exist to fabricate and assemble the major component, listed in alphabetical order by name.
Table 1. Export Cable Roles
Responsibility Level |
Job Positions |
---|---|
Factory-Level Management |
|
Design and Engineering |
|
Quality and Safety |
|
Factory-Level Work |
|
The employees fabricating a component may have to complete a workforce certification based on the scope of work. Certification needs specific to the component are listed in the table below in alphabetical order by name. Additional research is needed to align the certifications with a specific occupation and understand the training needs for certifications.
Table 2. Export Cable Job Certifications
Certification |
Length of Time |
Resource |
---|---|---|
Certified Manager of Quality/Organizational Excellence (CMQ/QE) |
10-15 years |
|
Certified Reliability Engineer (CRE) |
11 years |
|
Certified Quality Improvement Associate (CQIA) |
2 years |
|
Certified Quality Process Analyst (CQPA) |
2 years |
|
Certified Quality Technician (CQT) |
4 years |
|
Certified Welding Inspector (CWI) |
2-8 weeks |
|
Computer numerical control (CNC)Lathe Operations |
37 hours |
|
Computer numerical control (CNC)Lathe Programming Setup and Operations |
Varies by program |
|
Computer numerical control (CNC)Mill Operation |
38 hours |
|
Global Wind Organization Basic Safety Training (GWO BST) |
2 days |
https://www.globalwindsafety.org/standards/basic-safety-training-standard |
ICS: 29.020 Electrical Engineering |
Varies by program |
|
ISO 9001: 2015 Certified Lead Auditor |
2 weeks |
https://asq.org/training/iso-9001-2015-certified-lead-auditor-viso90012015cla |
ISO/AWI 15513: Cranes |
Varies by program |
|
Lean Certification |
8–16 weeks |
|
Milling I |
Less than a year |
|
National Commission for the Certification of Crane Operators (NCCCO) |
1 year |
https://www.nccco.org/nccco/certifications/tower-crane-operator/certification-overview |
Nondestructive Testing (NDT) |
8 months |
|
OSHA 10 |
2 days |
|
OSHA 30 |
4 days |
|
Six Sigma Green Belt Certification |
10 weeks |
https://www.sixsigmacouncil.org/six-sigma-green-belt-certification/ |
Supplier jobs represent the greater job market opportunity in offshore wind workforce across all job sectors. For every job created in these major component manufacturing facilities, there is an opportunity space to train and hire up to 5 five supplier jobs to produce subassemblies, parts, and materials. In addition, existing businesses with relevant skills and capabilities across the country participate in the offshore wind supply chain. The number of supplier jobs will depend on the level of domestic content in the supporting supply chain, with the numbers below assuming 25% to 100% domestic content (i.e., how many of these products are made in the United States instead of being imported). The figure below maps component-by-component flowcharts with a breakdown of workforce magnitude for each subassembly or subcomponent.
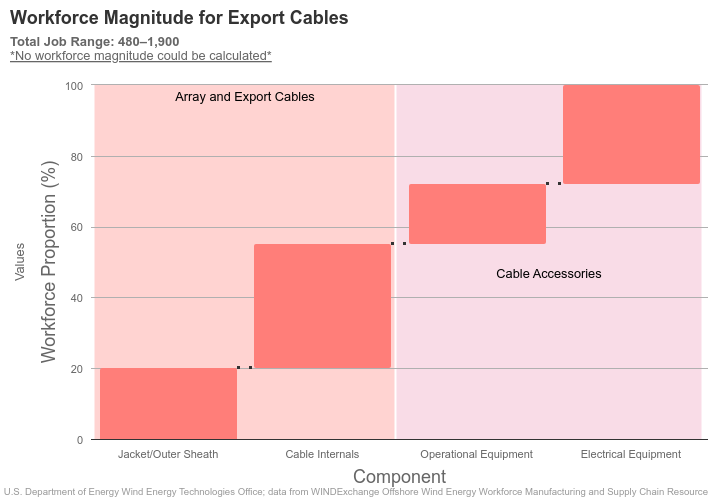
Monopiles
The figure below estimates the direct job needs in the major component manufacturing facility based on the number of workers needed, and facilities opening over time to fabricate components to reach a 30 GW by 2030 target. The jobs count below represent any person working in the facility to produce or oversee the fabrication and assembly, including tradespeople, mangers, engineers, and professional services.
The number of FTEs available is based on the number of direct FTE per facility multiplied by the number of facilities to produce supply 4–6 GW of projects per year. Direct FTEs are estimated from interviews and surveys of facility operators.
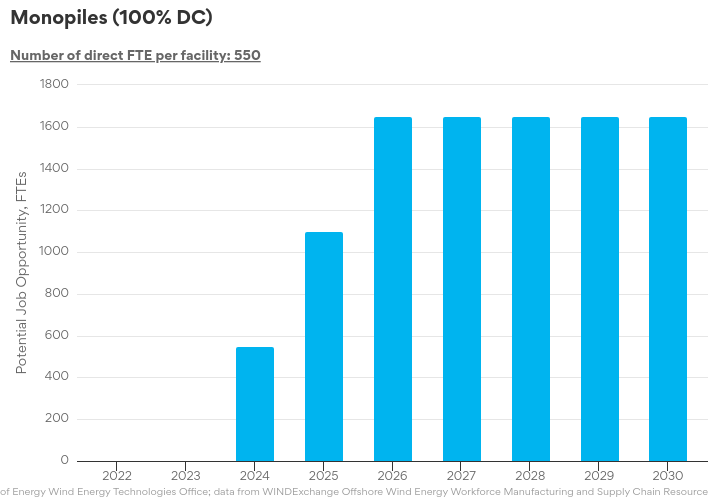
The workers in each major component facility include different types of roles with various levels of education and experience requirements. The table below shows four different workforce categories and lists the types of occupations that exist to fabricate and assemble the major component, listed in alphabetical order by name.
Table 1. Monopile Roles
Responsibility Level |
Job Positions |
---|---|
Factory-Level Management |
|
Design and Engineering |
|
Quality and Safety |
|
Factory-Level Work |
|
The employees fabricating a component may have to complete a workforce certification based on the scope of work. Certification needs specific to the component are listed in the table below in alphabetical order by name. Additional research is needed to align the certifications with a specific occupation and understand the training needs for certifications.
Table 2. Monopile Job Certifications
Certification |
Length of Time |
Resource |
---|---|---|
API 577: Welding Inspection and Metallurgy |
1–5 years |
|
ASME Practical Welding Technology |
8 days |
|
Certified Construction Manager (CCM) |
4–8 years |
|
Certified Quality Auditor (CQA) |
6–11 years |
|
Certified Quality Engineer (CQE) |
5–10 years |
|
Certified Welding Inspector (CWI) |
2-8 weeks |
|
Certified Welder Program |
1–4 years |
https://www.aws.org/certification/page/certified-welder-program |
Certified Manager of Quality/Organizational Excellence (CMQ/QE) |
10–15 years |
|
Global Wind Organization Basic Safety Training (GWO BST) |
2 days |
https://www.globalwindsafety.org/standards/basic-safety-training-standard |
ISO/AWI 15513: Cranes |
Varies by program |
|
National Commission for the Certification of Crane Operators (NCCCO) |
1 year |
https://www.nccco.org/nccco/certifications/tower-crane-operator/certification-overview |
OSHA 10 |
2 days |
|
OSHA 30 |
4 days |
|
Transportation Worker Identification Credential (TWIC) |
10–60 days |
Supplier jobs represent the greater job market opportunity in offshore wind workforce across all job sectors. For every job created in these major component manufacturing facilities, there is an opportunity space to train and hire up to 5 five supplier jobs to produce subassemblies, parts, and materials. In addition, existing businesses with relevant skills and capabilities across the country participate in the offshore wind supply chain. The number of supplier jobs will depend on the level of domestic content in the supporting supply chain, with the numbers below assuming 25% to 100% domestic content (i.e., how many of these products are made in the United States instead of being imported). The figure below maps component-by-component flowcharts with a breakdown of workforce magnitude for each subassembly or subcomponent.
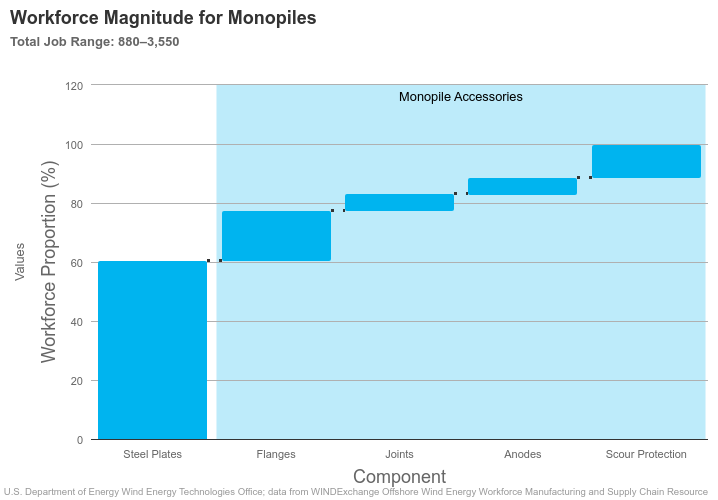
Nacelles
The figure below estimates the direct job needs in the major component manufacturing facility based on the number of workers needed, and facilities opening over time to fabricate components to reach a 30 GW by 2030 target. The jobs count below represent any person working in the facility to produce or oversee the fabrication and assembly, including tradespeople, mangers, engineers, and professional services.
The number of FTEs available is based on the number of direct FTE per facility multiplied by the number of facilities to produce supply 4–6 GW of projects per year. Direct FTEs are estimated from interviews and surveys of facility operators.

The workers in each major component facility include different types of roles with various levels of education and experience requirements. The table below shows four different workforce categories and lists the types of occupations that exist to fabricate and assemble the major component, listed in alphabetical order by name.
Table 1. Nacelle Roles
Responsibility Level |
Job Positions |
---|---|
Factory-Level Management |
|
Design and Engineering |
|
Quality and Safety |
|
Factory-Level Work |
|
The employees fabricating a component may have to complete a workforce certification based on the scope of work. Certification needs specific to the component are listed in the table below in alphabetical order by name. Additional research is needed to align the certifications with a specific occupation and understand the training needs for certifications.
Table 2. Nacelle Job Certifications
Certification |
Length of Time |
Resource |
---|---|---|
API 577: Welding Inspection and Metallurgy |
1–5 years |
|
ASME Practical Welding Technology |
8 days |
|
Certified Calibration Technician (CCT) |
5 years |
|
Certified Coating Applicator (CCA) |
4 years |
|
Certified Control Systems Technician (CCST) |
5–13 years |
|
Certified Electronics System Associate |
6 months |
https://certifiedelectronicstechnician.org/electronics-system-associate-exams-esa/ |
Certified Manager of Quality/Organizational Excellence (CMQ/QE) |
10-15 years |
|
Certified Electronics System Associate |
6 months |
https://certifiedelectronicstechnician.org/electronics-system-associate-exams-esa/ |
Computer numerical control (CNC)Lathe Programming Setup and Operations |
Varies by program |
|
Computer numerical control (CNC)Mill Operation |
38 hours |
|
Certified Reliability Engineer (CRE) |
11 years |
|
Certified Quality Improvement Associate (CQIA) |
2 years |
|
Certified Quality Inspector (CQI) |
2 years |
|
Certified Quality Process Analyst (CQPA) |
2 years |
|
Certified Quality Technician (CQT) |
4 years |
|
Drill Rig Operator National Commission for the Certification of Crane Operator |
4-10 years |
https://www.nccco.org/nccco/certifications/drill-rig-operator |
Global Wind Organization Basic Safety Training (GWO BST) |
2 days |
https://www.globalwindsafety.org/standards/basic-safety-training-standard |
ICS: 29.020 Electrical Engineering |
Varies by program |
|
ISO 9001: 2015 Certified Lead Auditor |
2 weeks |
|
ISO/AWI 15513: Cranes |
Varies by program |
https://asq.org/training/iso-9001-2015-certified-lead-auditor-viso90012015cla |
Lean Certification |
8-16 weeks |
|
Milling I |
Less than a year |
|
Mobile Crane Operations |
55 hours |
https://www.nccer.org/craft-catalog/mobile-crane-operations/ |
National Association of Manufacturers |
Varies by program |
https://www.nam.org/legal-expertise/manufacturing-institute/ |
National Commission for the Certification of Crane Operators (NCCCO) |
1 year |
https://www.nccco.org/nccco/certifications/tower-crane-operator/certification-overview |
National Occupational Competency Testing Institute |
Varies by program |
|
National Institute for Metalworking Skills |
Varies by program |
|
Nondestructive Testing (NDT) |
8 months |
|
OSHA 10 |
2 days |
|
OSHA 30 |
4 days |
|
OSHA Forklift Certification Course |
1 hour |
|
Six Sigma Green Belt Certification |
10 weeks |
https://www.sixsigmacouncil.org/six-sigma-green-belt-certification/ |
Surface Mount Technology Association (SMTA) |
1.5 days |
Supplier jobs represent the greater job market opportunity in offshore wind workforce across all job sectors. For every job created in these major component manufacturing facilities, there is an opportunity space to train and hire up to 5 five supplier jobs to produce subassemblies, parts, and materials. In addition, existing businesses with relevant skills and capabilities across the country participate in the offshore wind supply chain. The number of supplier jobs will depend on the level of domestic content in the supporting supply chain, with the numbers below assuming 25% to 100% domestic content (i.e., how many of these products are made in the United States instead of being imported). The figure below maps component-by-component flowcharts with a breakdown of workforce magnitude for each subassembly or subcomponent.
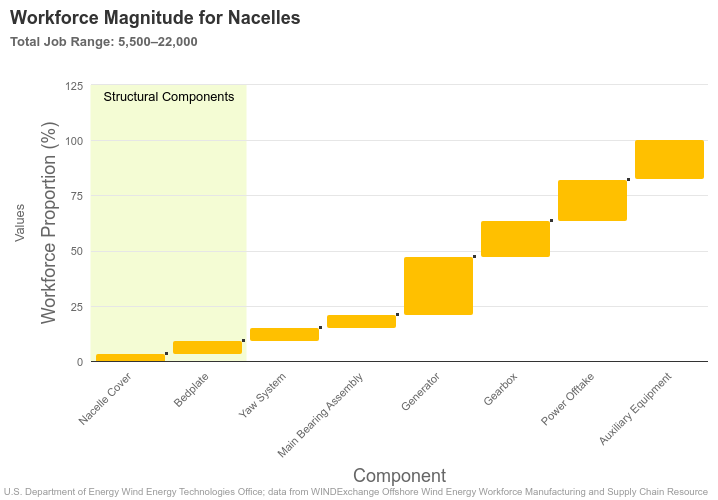
Towers
The figure below estimates the direct job needs in the major component manufacturing facility based on the number of workers needed, and facilities opening over time to fabricate components to reach a 30 GW by 2030 target. The jobs count below represent any person working in the facility to produce or oversee the fabrication and assembly, including tradespeople, mangers, engineers, and professional services.
The number of FTEs available is based on the number of direct FTE per facility multiplied by the number of facilities to produce supply 4–6 GW of projects per year. Direct FTEs are estimated from interviews and surveys of facility operators.
The number of FTEs available is based on the number of direct FTE per facility multiplied by the number of facilities to produce supply 4–6 GW of projects per year. Direct FTEs are estimated from interviews and surveys of facility operators.
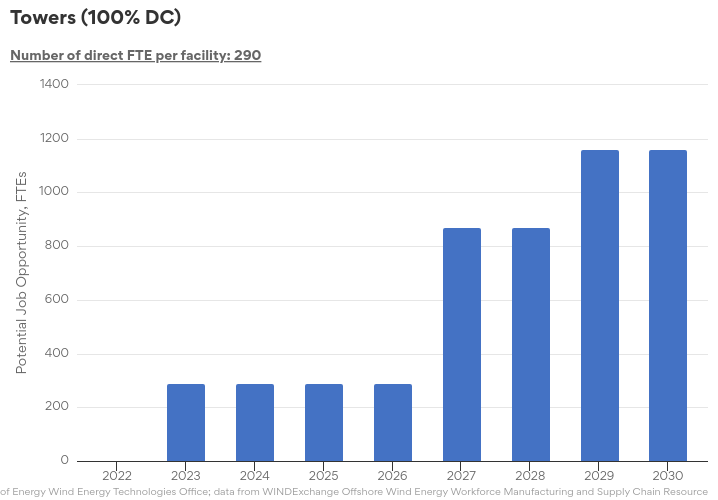
The workers in each major component facility include different types of roles with various levels of education and experience requirements. The table below shows four different workforce categories and lists the types of occupations that exist to fabricate and assemble the major component, listed in alphabetical order by name.
Table 1. Tower Roles
Responsibility Level |
Job Positions |
---|---|
Factory-Level Management |
|
Design and Engineering |
|
Quality and Safety |
|
Factory-Level Work |
|
The employees fabricating a component may have to complete a workforce certification based on the scope of work. Certification needs specific to the component are listed in the table below in alphabetical order by name. Additional research is needed to align the certifications with a specific occupation and understand the training needs for certifications.
Table 2. Tower Job Certifications
Certification |
Length of Time |
Resource |
---|---|---|
Certified Coating Applicator (CCA) |
4 years |
|
Certified Control Systems Technician (CCST) |
5–13 years |
|
Certified Construction Manager (CCM) |
4–8 years |
|
Certified Quality Inspector (CQI) |
2 years |
|
Certified Quality Technician (CQT) |
4 years |
|
Certified Quality Inspector (CQI) |
2 years |
|
Certified Quality Process Analyst (CQPA) |
2 years |
|
Certified Quality Improvement Associate (CQIA) |
2 years |
|
Certified Quality Improvement Associate (CQIA) |
2 years |
|
Certified Welding Inspector (CWI) |
2-8 weeks |
|
Certified Welder Program |
1-4 years |
https://www.aws.org/certification/page/certified-welder-program |
Computer numerical control (CNC)Lathe Operations |
37 hours |
|
Computer numerical control (CNC)Lathe Programming Setup and Operations |
Varies by program |
|
Computer numerical control (CNC)Mill Operation |
38 hours |
|
Certified Manager of Quality/Organizational Excellence (CMQ/QE) |
10-15 years |
|
Certified Reliability Engineer (CRE) |
11 years |
|
Drill Rig Operator National Commission for the Certification of Crane Operator |
4-10 years |
https://www.nccco.org/nccco/certifications/drill-rig-operator |
Global Wind Organization Basic Safety Training (GWO BST) |
2 days |
https://www.globalwindsafety.org/standards/basic-safety-training-standard |
ISO 9001: 2015 Certified Lead Auditor |
2 weeks |
https://asq.org/training/iso-9001-2015-certified-lead-auditor-viso90012015cla |
ISO/AWI 15513: Cranes |
Varies by program |
|
Lean Certification |
8-16 weeks |
|
Milling I |
Less than a year |
|
National Association of Manufacturers |
Varies by program |
https://www.nam.org/legal-expertise/manufacturing-institute/ |
National Commission for the Certification of Crane Operators (NCCCO) |
1 year |
https://www.nccco.org/nccco/certifications/tower-crane-operator/certification-overview |
National Occupational Competency Testing Institute |
Varies by program |
|
National Institute for Metalworking Skills |
Varies by program |
|
Nondestructive Testing (NDT) |
8 months |
|
OSHA 10 |
2 days |
|
OSHA 30 |
4 days |
|
OSMRE Blaster Certification |
3 years |
https://www.osmre.gov/sites/default/files/inline-files/OSM%2074%20exp%202024%20update%206.17.21.pdf |
Six Sigma Green Belt Certification |
10 weeks |
https://www.sixsigmacouncil.org/six-sigma-green-belt-certification/ |
Surface Mount Technology Association (SMTA) |
1.5 days |
Supplier jobs represent the greater job market opportunity in the offshore wind workforce across all job sectors. For every job created in these major component manufacturing facilities, there is an opportunity space to train and hire up to 5 five supplier jobs to produce subassemblies, parts, and materials. In addition, existing businesses with relevant skills and capabilities across the country participate in the offshore wind supply chain. The number of supplier jobs will depend on the level of domestic content in the supporting supply chain, with the numbers below assuming 25% to 100% domestic content (i.e., how many of these products are made in the United States instead of being imported). The figure below maps component-by-component flowcharts with a breakdown of workforce magnitude for each subassembly or subcomponent.
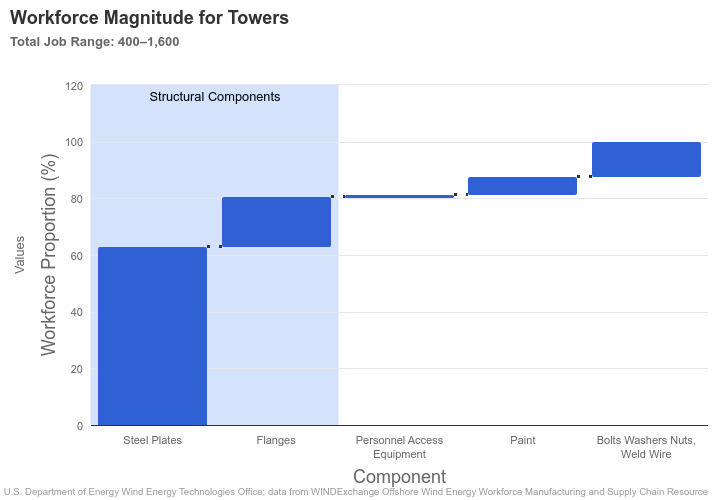
Transition Pieces
The figure below estimates the direct job needs in the major component manufacturing facility based on the number of workers needed, and facilities opening over time to fabricate components to reach a 30 GW by 2030 target. The jobs count below represent any person working in the facility to produce or oversee the fabrication and assembly, including tradespeople, mangers, engineers, and professional services.
The number of FTEs available is based on the number of direct FTE per facility multiplied by the number of facilities to produce supply 4–6 GW of projects per year. Direct FTEs are estimated from interviews and surveys of facility operators.
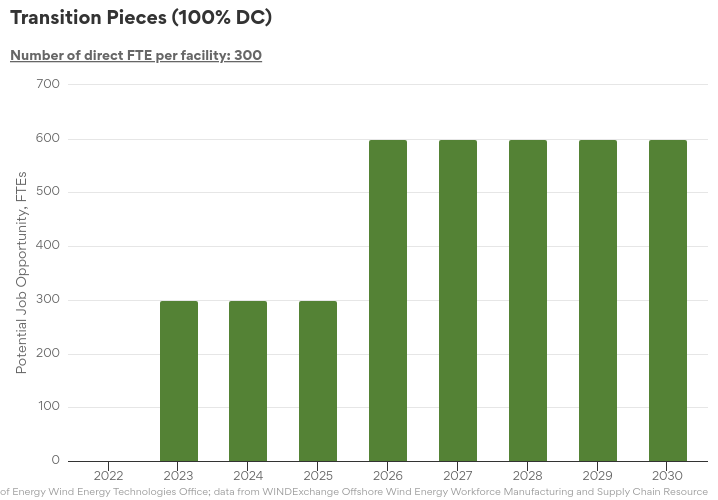
The workers in each major component facility include different types of roles with various levels of education and experience requirements. The table below shows four different workforce categories and lists the types of occupations that exist to fabricate and assemble the major component, listed in alphabetical order by name.
Table 1. Transition Piece Roles
Responsibility Level |
Job Positions |
---|---|
Factory-Level Management |
|
Design and Engineering |
|
Quality and Safety |
|
Factory-Level Work |
|
The employees fabricating a component may have to complete a workforce certification based on the scope of work. Certification needs specific to the component are listed in the table below in alphabetical order by name. Additional research is needed to align the certifications with a specific occupation and understand the training needs for certifications.
Table 2. Transition Piece Certifications
Certification |
Length of Time |
Resource |
---|---|---|
API 577: Welding Inspection and Metallurgy |
1-5 years |
|
ASME Practical Welding Technology |
8 Days |
|
Certified Construction Manager (CCM) |
4–8 years |
|
Certified Manager of Quality/Organizational Excellence (CMQ/QE) |
10-15 years |
|
Certified Quality Engineer (CQE) |
5–10 years |
|
Certified Quality Auditor (CQA) |
6–11 years |
|
Certified Welding Inspector (CWI) |
2-8 weeks |
|
Certified Welder Program |
1–4 years |
https://www.aws.org/certification/page/certified-welder-program |
Global Wind Organization Basic Safety Training (GWO BST) |
2 days |
https://www.globalwindsafety.org/standards/basic-safety-training-standard |
ISO/AWI 15513: Cranes |
Varies by program |
|
National Commission for the Certification of Crane Operators (NCCCO) |
1 year |
https://www.nccco.org/nccco/certifications/tower-crane-operator/certification-overview |
OSHA 10 |
2 days |
|
OSHA 30 |
4 days |
|
Transportation Worker Identification Credential (TWIC) |
10–60 days |
Supplier jobs represent the greater job market opportunity in offshore wind workforce across all job sectors. For every job created in these major component manufacturing facilities, there is an opportunity space to train and hire up to 5 five supplier jobs to produce subassemblies, parts, and materials. In addition, existing businesses with relevant skills and capabilities across the country participate in the offshore wind supply chain. The number of supplier jobs will depend on the level of domestic content in the supporting supply chain, with the numbers below assuming 25% to 100% domestic content (i.e., how many of these products are made in the United States instead of being imported). The figure below maps component-by-component flowcharts with a breakdown of workforce magnitude for each subassembly or subcomponent.
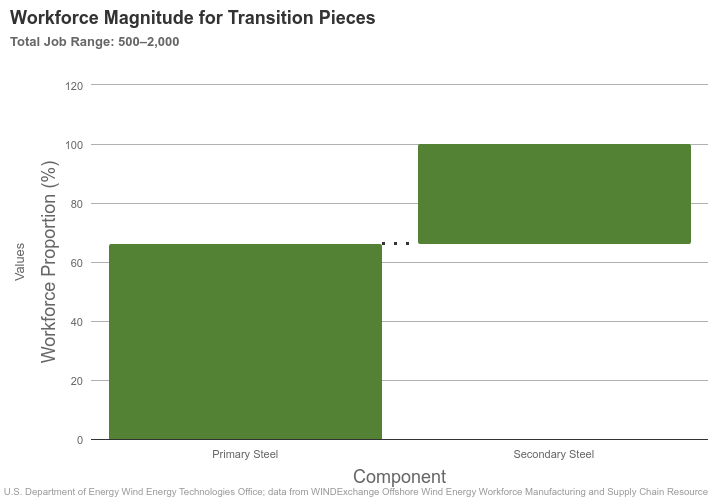
References
[1] Stefek, Jeremy, Chloe Constant, Caitlyn Clark, Heidi Tinnesand, Corrie Christol, Ruth Baranowski. 2022. U.S. Offshore Wind Workforce Assessment. Golden, CO: National Renewable Energy Laboratory. NREL/TP-5000-81798https://www.nrel.gov/docs/fy23osti/81798.pdf.
[2] Same as above.
[3] Shields, Matt, Ruth Marsh, Jeremy Stefek, Frank Oteri, Ross Gould, Noé Rouxel, Katherine Diaz, Javier Molinero, Abigayle Moser, Courtney Malvik, and Sam Tirone. 2022. The Demand for a Domestic Offshore Wind Energy Supply Chain. Golden, CO: National Renewable Energy Laboratory. NREL/TP-5000-81602. https://www.nrel.gov/docs/fy22osti/81602.pdf.
[4] Shields, Matt, Jeremy Stefek, Frank Oteri, Sabina Maniak, Matilda Kreider, Elizabeth Gill, Ross Gould, Courtney Malvik, Sam Tirone, Eric Hines. 2023. A Supply Chain Road Map for Offshore Wind Energy in the United States. Golden, CO: National Renewable Energy Laboratory. NREL/TP-5000-84710. https://www.nrel.gov/docs/fy23osti/84710.pdf.
Publication Information
This factsheet was sponsored by DOE Wind Energy Technologies Office and created by NREL to compile data and insights on manufacturing and supply chain opportunities within offshore wind energy industry.
If you would like to get involved in the Offshore Wind Workforce Network or feel your organization is misrepresented or not included in this factsheet, please contact us at WindWorkforce@nrel.gov.
This work was authored by the National Renewable Energy Laboratory, operated by Alliance for Sustainable Energy, LLC, for the U.S. Department of Energy (DOE) under Contract No. DE-AC36-08GO28308. Funding provided by U.S. Department of Energy Wind Energy Technologies Office. The views expressed in the article do not necessarily represent the views of the DOE or the U.S. Government. The U.S. Government retains and the publisher, by accepting the article for publication, acknowledges that the U.S. Government retains a nonexclusive, paid-up, irrevocable, worldwide license to publish or reproduce the published form of this work, or allow others to do so, for U.S. Government purposes.
Return to top